TAMPA BAY'S PREMIER
DIGITAL PRINT SUPPLIER
National UV Supply Company, Inc. (NUVS), established in 1981, serves the offset and digital printing industry, focusing on delivering cutting-edge technology to enhance quality, speed production, and minimize industrial waste. With a 33-year commitment, our aim is to source innovative products, provide comprehensive education and support, including pre-investment training, and offer ongoing educational programs to keep abreast of advancements.
NUVS stands behind all equipment and products, ensuring customer satisfaction and peace of mind. We invite current and prospective clients to tour our 16,000 sq. ft. facility, showcasing multiple production lines featuring the latest technology. Backed by technicians with over 50 years of collective industry experience, we prioritize personalized consultations to understand each client's needs, goals, and future plans, fostering a stress-free and informed decision-making process.
Leaders in Digital Printing Excellence
VANGUARD PRINTERS
Flexible large-format printers and routers support a wide range of engineering, architectural, and graphics applications. Whether you're printing point-of-sale graphics, outdoor banners, trade show displays, digital photo enlargements, fine art giclée, or have router requirements, we have the solutions for your needs. You're welcome to visit our demo room for hands-on demonstrations. Please contact our customer service department for additional information and to schedule your visit.
DIRECT COLOR SYSTEM PRINTERS
UV ROLLER COATERS
XDC-Micro Coater
The
VividCoater XDC-Micro™
is a low-maintenance, ultraviolet-cured coating system that delivers a high-quality finish to printed sheets. Enhancing colors for both digital and offset prints, it provides the on-demand print market with cost-effective, expressive products. With a footprint under 3'x3' (100 cm square) and a variable speed of up to 2700 sheets per hour, the XDC-Micro™ is easily maneuverable through standard doors. Featuring variable coating thickness and speed control, along with user-friendly elements like easy set handles, standard IR, wiper blade, and vacuum hold down, the machine ensures quick setup and operation.
Features
Electrical: Amperage 30A breaker required, Voltage 208-240V, 50/60Hz, 1 phase
Max Stock Size: 20.75" W (53 cm)* Unlimited (standard tray holds up to 18" (457mm)
Coater Size (LxWXH): 29.25"x35.25"x34.25" (74x87x87 cm)
Coater weight: 420 lbs ( 191 kg)
Coating Capacity: 9 lb (4.1 k) buckets (5000+ sheets)
Coating Thickness: 5 to 25.4 microns
Coating Technology: 100% UV Curable/roll flood
Coating Roller: Proprietary EDPM
Coating Finish: Smooth
Miscellaneous Information
- Vacuum hold down
- Standard IR
- Coats stock from 128 - 450 gsm
- Variable speed, up to 2700 sheets per hour
- Polished chrome metering and bottom rollers
- Wiper blade
- Air-cooled direct-focused UV Lamp and IR
- Forward/Reverse controls for easy clean up
- Easy set handles for pressure control/wiper blade
isg uv roller coater
National UV Supply Company offers top-tier OEM and custom UV coating machines, feeders, and stackers to the printing industry, all designed and built in the USA. Crafted to meet industrial standards, our products enable customers to sustain high-volume production continuously, alleviating concerns about breakdowns.
Easy Access
The coating container features a hinged lid for easy access, facilitating mixing of the coating before use. Additionally, an industrial pump ensures a constant flow of chemistry for seamless operations.
Bearing Protection
Bearing protection is ensured through the use of Nylon End Dams, safeguarding against UV chemistry and effectively reducing wear and maintenance requirements.
Industrial Bearings
Industrial bearings and spring-loaded application and metering rollers are incorporated to minimize roller wear and offer operators precise pressure controls, allowing for fine-tuning of the coating application.
Optional Thin Strip Removal System
An optional "Thin Strip Removal System" is available, specifically designed for coating text weight stocks as low as 80 lbs, enhancing versatility and performance.
Easy Cleaning
Personnel can easily access the rollers for cleaning at the end of the day, ensuring convenient maintenance procedures.
xdc uv coaters
The XDC coater is offered in three sizes for various coating profiles (18.80", 26.5", and 29.5" wide). It boasts user-friendly touch screen controls and an on/off lever for the doctor blade. Additionally, a deep pile feeder is available, allowing for integration into existing lines in the field. A unique feature of this coater is its infrared (IR) capability, which preheats substrates before curing, particularly useful for challenging-to-adhere digital inks.
XDC 480 UV Coater 18.8" wide
Features:
Electrical: 208/220-240V 1 phase / 60Hz / 55A
Speed: 5900’/hour (1800m/hour)
Max Stock Size: 18.80”W x 20.5”L
Stock Weight: 157-450 gsm
*Changes according to paper quality
Dimensions:
Length: 119” (302 cm)
Width: 36” (92 cm)
Height: 44” (112 cm)
Weight: 1190 lbs (540 kg)
Miscellaneous Information:
- Standard with touch screen controls for easier use
- UV and IR (3 bulbs)
- Deep pile feeder - 18” capacity
- CE approved
- Double sheet detector
- Stainless steel doctor blade (on/off lever)
- Three roller coating application system
- Easy set lever for adjusting roller pressure settings and doctor blade
Note: Automatic feed requires compressed air. External ventilation or air purification highly recommended.
XDC 660 UV Coater 25" wide
Features:
Electrical: 208/220-240V 1 phase / 60Hz / 55A
Speed: 5900’/hour (1800m/hour)
Max Stock Size: 26.00”W x 20.5”L
Stock Weight: 157-450 gsm
*Changes according to paper quality
Dimensions:
Length: 125”
Width: 44” (112 cm)
Height: 45” (114 cm)
Weight: 1300 lbs
Miscellaneous Information:
- Standard with touch screen controls for easier use
- UV and IR (3 bulbs)
- Deep pile feeder - 18” capacity
- CE approved
- Double sheet detector
- Stainless steel doctor blade (on/off lever)
- 3 roller coating application system
- Easy set lever for adjusting roller pressure settings and doctor blade
Note: Automatic feed requires compressed air. External ventilation or air purification highly recommended.
XDC 750 UV Coater 29.5" wide
Features:
Electrical: 208/220-240V 1 phase / 60Hz / 55A
Speed: 5900’/hour (1800m/hour)
Max Stock Size: 26.00”W x 25.0”L
Stock Weight: 157-450 gsm
*Changes according to paper quality
Dimensions:
Length: 125”
Width: 52”
Height: 45”
Weight: 1800 lbs
Miscellaneous Information:
Standard with touch screen controls for easier use
UV and IR (3 bulbs)
Deep pile feeder - 18” capacity
CE approved
Double sheet detector
Stainless steel doctor blade (on/off lever)
3 roller coating application system
Easy set lever for adjusting roller pressure settings and doctor blade
Note: Automatic feed requires compressed air. External ventilation or air purification highly recommended.
620A UV Spot Coater
DLG coater is available as a flood or spot coater. The flood coater comes in a two size (18" and 24") coating profile. The spot coater is a 24" coating profile. User-friendly with touch screen controls, deep pile feeder and an optional stacker. This coater has a unique feature IR (infrared) to preheat substrate prior to cure for those difficult-to-adhere-to digital inks.
Features
Electrical: 220-240V 3phase/60Hz/80A
Speed: up to 5500 sph
Max Stock Size: 24.25”W(62cm) * 17.7”(45cm) (spot coater)
Stock Weight: 80-350 gsm
Length: 118” (300 cm)
Width: 44” (110 cm)
Height: 55.25” (140 cm)
Weight: 2975 lbs (1350 kg)
Miscellaneous Information
- Standard with touchscreen controls for easier use
- UV lamp (one standard, second optional)(Spot Coater comes with 2 standard)
- IR lamp as standard
- Three rollers with reverse and variable roller speed ratio control provides best coating results
- Pneumatic automatic receding stacker on AS models and Spot Coater
- Air knife optional for assistance with thin stocks (above 80 gsm)
Note: All models require compressed air. External ventilation or air purification highly recommended.
American UV Coater
The American Ultraviolet Coater offers the Spectra-Coat UNI, an offline, sheet-fed system meeting modern standards with coating widths of 20/25/30/40 inches, accommodating all media types. It includes various features and optional feeders and stackers. With a legacy in UV technology since 1960, we prioritize innovation and quality, providing competitive pricing and comprehensive technical support. Our Spectra-Coat UV Coating System Solutions feature standard digital/offset and wide-format UV coating equipment, with custom sizes available, ensuring superior performance tailored to industry needs.
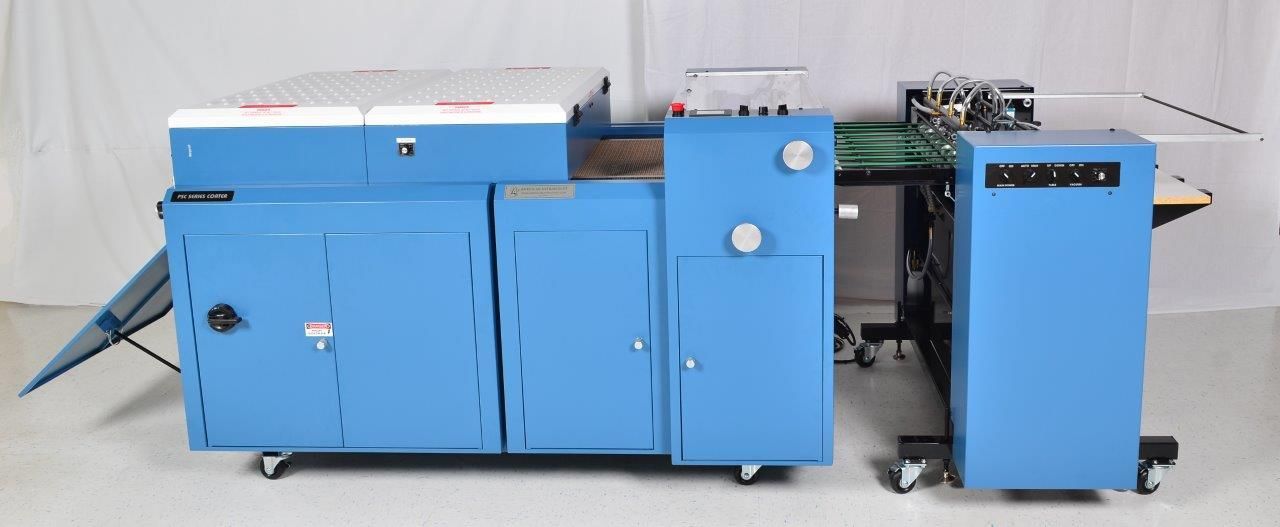
Information About Feeders
- Minimum sheet size: 5” x 7”
- Maximum sheet size: 22” x 28” (additional sizes available)
- Paper weight: 20# bond to 22 point cover; and other substrates and thicknesses
- Pile height: 18”
- Height: 44”
- Width: 43”
- Length: 38”
- 115 Volts – 20 Amps – 60 Hz
- Conveyor speed: Up to 5,000 sheets per hour, depending on sheet size
AUV Wide Format UV Roller Coater
Introducing the AUV Wide Format 80" UV Coater, tailored for flatbed printers employing diverse ink types such as UV, solvent, and water-based. With coating widths of 60/80 inches and customizable sizes, this system offers superior, high-speed, heavy-duty performance, enabling market expansion and enhancing profitability in existing markets.
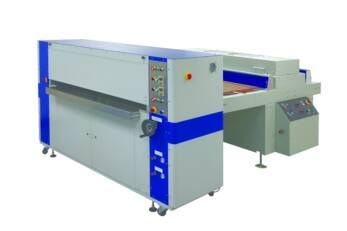
STILL HAVE QUESTIONS?
CHECK OUT OUR UV COATER FAQs.
We have supported our customers for over 29 years by testing and reviewing the latest technology available today from multiple manufacturers. With the fast-changing market in the printing industry—especially with digital technology—it is important to recognize there are many UV roller coating manufacturers and UV coaters to choose from. You are welcome to contact our customer service department for a UV coater recommendation with your specific application in mind. We have listed a few popular questions that you may find useful.
How do I choose the right UV roller coating equipment for my needs?
There are several key considerations when selecting production equipment: cost, support, quality, speed, and user-friendliness. Cost-wise, it's essential to invest in UV roller coating equipment that meets both current needs and future requirements, as cutting corners can lead to costly repairs and downtime. Adequate support, including hands-on training for personnel, is crucial for safe and productive operation. Choose suppliers with a reputation for good support and readily available wearable parts. Quality should ultimately be judged by customer feedback, so involving them in the evaluation process is important. Production speed varies depending on equipment, with off-line coaters typically ranging from 1,000 to 5,000 sheets per hour for a 13” x 19” sheet. Adding features like automatic feeders or landscape feeding can significantly increase speed. Finally, prioritize user-friendliness by ensuring thorough training upon installation or visiting the vendor for demonstrations before making a purchase, particularly for automatic feeders and stackers.
How do I choose a suitable substrate (printable materials) for UV coating?
Substrate selection plays a crucial role in achieving optimal gloss levels with UV coating. High-quality coated stocks retain the UV coating on the surface, resulting in optimal gloss. Conversely, poorly coated substrates may cause the UV coating to penetrate or absorb unevenly, leading to subpar gloss levels and a splotchy appearance. It's advisable to conduct tests using various substrates to identify the best-performing option.
Which UV coating is best suited for my digital printer/copier?
Due to the diversity of manufacturers for digital printing and copying equipment, as well as the multitude of production settings available, we advise discussing your specific application with one of our technicians. Please provide the equipment manufacturer's name, model number, production settings, and details about the substrate to be used for a tailored recommendation.
Can you use the same UV coating on any digital and offset printed substrate?
Unfortunately, manufacturers utilize various methods to apply inks to substrates, employing different ink or dye systems. Consequently, UV coating manufacturers must tailor their chemistry to ensure proper printability, flow out, and adhesion characteristics. By analyzing your specific application, we can recommend the most suitable UV chemistry available today. While it's possible to use the same UV chemistry for both offset and digital printing, this depends on the type of equipment you have.
Why use a UV coater instead of aqueous coating or varnishes?
The primary reason for choosing UV coatings is their superior physical characteristics, particularly the high gloss level compared to conventional varnishes or aqueous-based systems. UV coatings also offer significantly better abrasion or scuff resistance, reducing the likelihood of USPS bounce backs caused by address scuffing. Moreover, UV coatings provide superior chemical resistance, making them ideal for products that are handled frequently or may come into contact with liquids, such as menus, postcards, and business cards.
Will UV coaters reduce my production speed?
UV coatings dry and cure in milliseconds, enabling fast production with minimal drying space requirements. This technology allows for efficient throughput and rapid turnaround times in production processes.
I don't want to increase my "VOC" (Volatile Organic Compounds) output. I want to become as "environmentally friendly" as possible. How will using a UV coater impact my goal?
UV curable coatings virtually contain no VOCs (Volatile Organic Compounds), making them environmentally friendly. When properly cured, UV coatings are considered "Zero VOC" products. This attribute has led many printing facilities, including those for labels, folding cartons, commercial, and publication, to adopt UV technology as a means to enhance their environmental friendliness.
Sometimes the coating looks different when I start the UV coater. Why?
There are several reasons why UV coatings may vary in appearance from one application to the next, with the two most common being:
Inadequate mixing of the chemistry before use: Thoroughly mixing UV chemistry before application is crucial for optimal results. Proper mixing ensures that the components work together effectively, resulting in good flow, fast and complete curing, and adhesion to the substrate. Failure to mix the chemistry properly can shorten its lifespan and lead to product waste. Manual mixing for one to two minutes is recommended, as high-speed mixers are not advised.
Temperature fluctuations outside the normal range of 70 - 84 degrees F: If the temperature falls below 70 degrees, the chemistry may flow slowly, leading to "orange peel" texture, reduced gloss, and possible imperfections. Using a 5-gallon drum heater can help overcome this issue. On the other hand, temperatures above 82 degrees can decrease viscosity, resulting in reduced chemistry transfer to the substrate. Symptoms include diminished gloss, scuff resistance, and a splotchy appearance on marginally coated stocks. To ensure optimal results, maintain the chemistry in a controlled environment.
SCREEN PRINTING EQUIPMENT
Flexible large-format printers and routers support a wide range of engineering, architectural, and graphics applications. Whether you're printing point-of-sale graphics, outdoor banners, trade show displays, digital photo enlargements, fine art giclée, or have router requirements, we have the solutions for your needs. You're welcome to visit our demo room for hands-on demonstrations. Please contact our customer service department for additional information and to schedule your visit.
PRE-PRESS PRODUCTS
Discover the pinnacle of pre-press silkscreening excellence at National UV Supply Company. From premium emulsions to high-quality squeegees, explore our comprehensive collection for unmatched printing precision. Elevate your print game today!
Frames
Aluminum and wood frames in multiple popular sizes.
Fabric/Mesh
We offer a wide variety of meshes in stock, available for purchase by the yard, in 10-yard lengths, or 30-yard lengths. To help you select the appropriate mesh for your screen printing needs, please contact our customer service department.
Regarding mesh selection for textile printers, ink manufacturers and screen printers may have their own preferences. However, we can provide general recommendations:
- Athletic Inks: 62-85 mesh
- Glitter: 38 mesh
- Maxopake: 74-125 mesh
- Process: 305-355 mesh
- Shimmers: 60-86 mesh (Black: 110 mesh)
- Ultrasoft Inks: 86-305 mesh
- White Ink: 68-230 mesh (New 81sd allows ink flow)
- Solvent/UV: 230 mesh and higher
When creating your own mesh selection list, consider the following: lighter color materials require less ink layer, so higher mesh counts are suitable, while darker color materials need thicker ink layers, so lower mesh counts are recommended. Thicker ink layers also require longer cure times.
For manual press printers, mesh counts between 38 and 125, possibly up to 158, are recommended to avoid excessive effort when pushing ink through.
Automatic press owners have more flexibility and can utilize the full range of mesh counts.
Nutralyze Fabric Degreaser
Nutralyze screen printing degreaser is a highly concentrated degreasing and wetting agent suitable for all screen fabrics, particularly as a prep for conventional direct emulsion on coarser mesh. While it excels at degreasing new mesh, it lacks abrasives for roughening the fabric. Proper use of Nutralyze reduces pinhole incidence and enhances coating retention characteristics. Before application, ensure any ink or stencil stains are removed. For optimal economy, dilute at a ratio of 1 part Nutralyze to 10 parts water, though a 1:3 ratio provides ideal results. Application with a sponge or 3M pad brush is recommended, with the latter aiding in mesh abrasion. NUTRALYZE offers excellent sheeting and degreasing properties and is compatible with both soft and hard water, controlling spotting effectively. It's highly cost-effective, non-hazardous, and has a pleasant odor. Available in gallon and 5-gallon sizes, with gallon pricing at $27.12 with free shipping and 5-gallon pricing at $55.88 (shipping charges apply; contact for details).
Dual Cure Emulsion 6000G
Dual Cure Emulsion 6000G is a versatile diazo/photopolymer (dual cure) emulsion compatible with both solvent and water-based systems. It is ideal for various applications, including water-thinnable UV and water-based graphics inks, conventional UV inks, textile printing, and commercial applications. Offering outstanding resolution, definition, and high abrasion resistance, it contains 37% solids (sensitized) and exhibits exceptional resistance to humidity.
Before application, it's crucial to clean and degrease the screen mesh thoroughly to remove any oils, grease, ink stains, or contaminants that may interfere with consistent coating and stencil integrity. Ink stains can be effectively removed using NSC Haze/Ghost Remover, while NSC Degreaser helps eliminate mesh contaminants. After cleaning, the screen should be rinsed well with water and allowed to dry completely.
The diazo sensitizer, provided with each container of 6000G, should be dissolved in water and then added to the emulsion, followed by thorough stirring to ensure proper dispersion. Coating should be performed using a sharp-edged coater, with one coat applied to each side of the screen for optimal results. Additional coats may be necessary for thicker applications on coarser meshes.
Drying the coated screen is critical, requiring conditions of 86 to 104 degrees F and 30% to 40% relative humidity, with adequate air ventilation. An enclosed screen drying cabinet with heated airflow can aid in maintaining these conditions and preventing contamination.
Exposure times vary depending on mesh type, with guidelines provided in the exposure table. It's essential to use a light source specifically designed for screen printing, as exposure time can be affected by the light's output and distance from the vacuum frame.
After exposure, the image should be washed out using a cold water spray, followed by blotting and drying the screen in a horizontal position. Reclaiming the screen involves removing excess ink, ink residue, and stencil material using suitable solvents and high-pressure washing.
Proper storage and handling are essential for maintaining emulsion quality. Unsensitized emulsion should be stored in a cool, dry area, while sensitized emulsion has a shelf life of approximately two months under similar conditions. Coated screens can be stored for up to one year in a light-safe area with controlled temperature and humidity.
For exposed coated screens stored for over two hours, it's advisable to place them in a drying cabinet briefly before exposure to ensure optimal results.
Silkscreening Emulsion 6500G
Fast Exposing Diazo-Photopolymer Screen Printing Photo Emulsion 6500G is a versatile dual-cure emulsion designed for solvent-based and UV inks, offering superior resolution, definition, and wide exposure latitude. With excellent solvent resistance and easy reclaiming, it provides exceptional durability and faster exposure times compared to conventional diazo emulsions. With a high solids content of 39%, it enables quick stencil buildup for efficient printing.
Before application, thorough cleaning and degreasing of the screen mesh are essential to ensure consistent coating and prevent stencil breakdown. Ink stains can be effectively removed using NSC Haze/Ghost Remover and NSC Degreaser, followed by rinsing and drying the screen completely.
Sensitizing involves dissolving the diazo sensitizer in water and mixing it with the emulsion, followed by thorough stirring and allowing air bubbles to dissipate. Proper coating entails applying one or two coats to both sides of the screen, with additional coats for thicker applications on coarser meshes. Drying the coated screen in a controlled environment with adequate ventilation is crucial for optimal results.
Exposure times vary depending on mesh type, with guidelines provided in the exposure table. Washing out the image involves spraying with cold water and rinsing until clear, followed by blotting and drying the screen horizontally. Reclaiming the screen involves removing excess ink and stencil residue using suitable solvents and a high-pressure washer.
For storage and handling, unsensitized emulsion should be stored in a cool, dry area, while sensitized emulsion has a shelf life of approximately two months under similar conditions. Coated screens can be stored for up to one year in a light-safe area with controlled temperature and humidity.
It's recommended to briefly place exposed coated screens in a drying cabinet before exposure if stored for over two hours under specified conditions.
Squeegee
The Straight Edge squeegee is a versatile tool commonly utilized in graphic and textile printing, renowned for its exceptional wear and solvent resistance, ensuring prolonged use. It comes in various configurations to meet specific printing needs:
Single Durometer: Featuring a single edge, this squeegee is a staple in graphic and textile printing. It offers durability and longevity while providing consistent performance.
Dual Durometer: Combining a soft printing edge with a hard backing, this option prevents blade roll over, maintaining precise blade angle for superior ink shear and print quality.
Triple Durometer: Engineered with two soft edges and a hard backing in between, this squeegee excels in achieving critical ink shear. It ensures proper blade angle without roll over, enhancing print accuracy and consistency.
POST-PRESS PRODUCTS
RC-ERC50 is the most concentrated decoating agent for all types of direct, direct/indirect, and capillary stencil types. Simply follow the dilution table to balance the desired mixture for performance and economy.
MIXTURE TABLE FOR FAST REMOVAL OF COATING:
TABLE USAGE:
- For RC-ERC50 with water: 8 oz. RC-ERC50 to 128 oz. (1 gallon) of water
- 32 oz. RC-ERC50 (1 quart) to 4 gallons of water
- 128 oz. RC-ERC50 (1 gallon) to 16 gallons of water
FOR ECONOMICAL SAVINGS:
TABLE USAGE:
- 3 oz. RC-ERC50 to 128 oz. (1 gallon) of water
- 32 oz. RC-ERC50 (1 quart) to 10 gallons of water
- 128 oz. RC-ERC50 (1 gallon) to 42 gallons of water
NOTE: Mix desired solutions as above or between those ratios to suit your particular needs.
ADVANTAGES OF RC-ERC50:
It costs less to ship than pre-mixed emulsion removers. Additionally, it does not coagulate or re-crystallize like powder crystals. Overall, it is easier to handle because it requires no mixing and simply goes into solution when water is added.
EXPERIENCE THE FULL RANGE OF
ON-PRESS PRODUCTS WE HAVE TO OFFER
Discover the vibrant world of screen printing with National UV Supply Company! Dive into our comprehensive selection featuring UV Screen Printing Inks, Textile Screen Printing Inks, and WM plastics. Elevate your printing projects with our premium products, designed to deliver stunning results. Unleash your creativity and explore the endless possibilities of on-press screen printing with us today!
UV Screen Printing Inks
Point of Purchase (POP) Series
The POP series is a high-performance, fast-curing UV screen printing ink specifically formulated for point-of-purchase applications. POP provides printers with an ink system for multiple uses on a wide variety of substrates. POP offers opacity and high gloss while maintaining a rapidly curing surface with excellent outdoor durability.
Performance Properties:
- Adhesion to a wide variety of substrates
- Superior opacity for color trapping
- Non-blocking, high-slip finish for easy handling
- Superb water and abrasion resistance
- Flexible for multi-layer applications/die-cutting
- N-VP and heavy-metal free
- Compatible with UP Series
Printing:
Mix ink well prior to use. While supplied in a press-ready condition, POP may be reduced by up to 10% with 1004 Universal Thinner. Care should be taken to print the ink at optimal temperatures of 70-90°F (21-27°C). Cool ink will have a heavier viscosity and will not flow properly. Hot ink will have lower viscosity, resulting in poor definition and decreased opacity.
Coverage:
3,200 to 3,600 square feet per gallon based on an ink deposit of 0.40-0.60 mil, dependent on color and printing conditions.
Curing:
Ink will cure well when printed through 355 (140cm) plain weave polyester mesh or finer. POP's optimal cure window of 125-150 mJ/550-650 mW is generally achieved with one 200-Watt per inch mercury vapor lamp at belt speeds between 70-90 feet per minute (21-27 m/min). This should provide thorough curing of the product. Cure speeds may vary as thicker material and dark surface colors require more energy. Adhesion should be a minimum of 95% from the curing unit with final adhesion developing within six hours of initial polymerization. Coarser fabrics can be utilized; however, cure parameters may need to be adjusted for increased ink film. If a loss of gloss or adhesion due to insufficient cure is noticed, the use of 5-10% of POP Overprint/Mixing Clear will increase light penetration and improve cure. Although the cured ink film has been engineered to optimize processing and handling, the printer must assume responsibility for pre-testing and qualifying the parameters for stacking printed parts prior to each run. The intensity of cure, weight or caliper of the material, and/or elevated ambient temperatures and humidity of the printing and storage environments will influence block resistance.
Recommended Substrates:
- Pressure Sensitive Vinyl
- Top-Coated and Print-Treated Polyesters
- Polystyrene
- ABS
- Polycarbonate (not for use with adhesives)
- Rigid Vinyl
- Coated and Uncoated Paper
- PETG
- Polyethylene Coated Card Stock
- Expanded Foam PVC (Sintra®, Celtec®)
- Foam Board
- Acrylic
- Fluted Polyolefins*, Polyethylene Sheet*
*With the use of Adhesion Promoters (1534 at 3% or 11939 at 3%), Renegade POP will adhere to fluted polyolefins such as Coroplast® and polyethylene sheet. Best adhesion forms after a six (6) hour post-cure. The modified ink’s shelf life is at least 3 days. Either adhesion promoter provides excellent water resistance. Light fastness at full strength and cured properly, POP colors are formulated to withstand 2-3 years of exterior exposure. The use of POP Overprint/Mixing Clear will increase the duration of outdoor durability. For all applications which will be exposed for up to 3 years, it is recommended that a premium grade, calendared vinyl be used. Factors which will alter the outdoor durability of the ink include, but are not limited to: substrate grade/age, poor cure of ink film, formulas, directional positioning, ink film deposit, exposure to excessive abrasives, and air pollutants. Under no circumstances should colors requiring long-term durability have mixing clear or white added to the formula. In addition, we do not recommend using less than 5% of any color in a blended formula for outdoor applications. Colors which should not be used for outdoor applications are CMS 164 Red BS, CMS 114 Orange, 180 Warm Red, and 131 Brilliant Orange. For very light fast applications requiring orange, blue-shade red, green-shade yellow, and/or medium-shade yellow, we recommend using POP+ BS Red Toner, POP+ GS Yellow Toner, POP+ 111 Lemon Yellow, and POP+ Orange Toner when small quantities of red, yellow, and orange are required for tinting white for pastel shades. The Polymeric color match system in many cases is not recommended for long-term exterior exposure due to many pastels and transparencies in the system. When using the color match system, contact Polymeric Imaging Inc. directly for possible color match recommendations.
Metallics:
Use the Metallic Mixing Clear to prepare metallic ink as its increased viscosity helps ensure a good particle suspension and extended shelf life.
Recommended mixing ratios by weight are:
- 28% Gold Paste
- 12% Silver Paste
- For optimum coverage and opacity, use 280-305 (110-120cm) plain weave mesh. Use Solar Shield Clear for extended weatherability and to improve the non-tarnishing properties of the product.
Additives:
- 1004 Universal Thinner - up to 10% as needed
- 13973 Static Cling Modifier - 2% as needed
- 1534 Adhesion Promoter - 3% as needed
- 11939 Adhesion Promoter - 3-5% as needed
- 2980+ Catalyst - 3% as needed (will gel in 4 hours)
Precautions:
Read the material safety data sheet prior to processing. It contains instructions for precautions when handling inks. If ink comes in contact with skin, wipe ink off with a clean, dry cloth (do not use solvent). Wash and rinse the affected area with soap and water.
Process Printing:
For superior halftone reproduction, halftones are available in a range of density levels. Additional control of density may be achieved with the use of GP MV HT Base. For best results, 380 (150cm) or finer mesh and a smooth, thin stencil coating should be utilized with process printing.
Storage:
Care should be taken to store ink in tightly-closed containers located in a cool (60 - 80°F / 15 - 27°C), dark place. After long production runs, excess ink from the screen should be properly disposed of. With suitable conditions, unopened ink is expected to have a shelf life of approximately twelve (12) months from the date of manufacture.
Color Availability:
POP Series is available in twenty opaque standard colors. Custom matches, metallic, fluorescent*, and transparent colors are obtainable upon request.
Pantone Matching System® Colors:
The nine Pantone® approved Color Matching System (CMS) shades are used to simulate the Pantone® Color Specified colors. Formulas were designed for maximum opacity and are available in book or Imaging Color Source Software formats.
A. Warranty Liability Limited to Purchase and Installation Costs:
Notwithstanding anything provided herein or any other written material to
the contrary, Polymeric only warrants the purchase price and costs of installation. POLYMERIC SHALL HAVE NO LIABILITY OR OBLIGATION TO ANY USER, BUYER, PURCHASER, DISTRIBUTOR, OR OTHER PERSON OR ENTITY FOR ANY SPECIAL, DIRECT, INDIRECT, INCIDENTAL, OR CONSEQUENTIAL DAMAGES, HOWEVER CAUSED, INCLUDING WITHOUT LIMITATION, PERSONAL INJURY, LOSS OF BUSINESS, LOSS OF PROFIT, OR OTHER DAMAGE, whether or not the buyer shall have informed Polymeric of the possibility or likelihood of any such damages.
B. Limitation of Implied Warranty and Fitness for a Particular Purpose:
POLYMERIC’S WARRANTY IS GIVEN IN LIEU OF ALL OTHER WARRANTIES, EXPRESS OR IMPLIED, INCLUDING BUT NOT LIMITED TO AN IMPLIED WARRANTY OF FITNESS FOR A PARTICULAR PURPOSE, AN IMPLIED WARRANTY OF MERCHANTABILITY, AND ANY OTHER IMPLIED WARRANTY ARISING OUT OF A COURSE OF DEALING, PERFORMANCE, CUSTOMER USAGE, OR TRADE.
MIX INK WELL BEFORE USE. Follow any indications on the package, ask for the safety data sheets, and always follow the indications contained therein. In case of doubt, please contact our Technical Service department.
POP+ Series
POP+ is a UV-curable screen printing ink formulated specifically for substrate adhesion performance. The adhesion properties of POP+ eliminate the need to purchase more costly ink and/or catalysts for substrates to which former multipurpose inks were not ideally suited. POP+ is the broadest ink system of its type, offering flexibility for pressure-sensitive vinyl applications with the unique versatility to adhere to HDPE and fluted polyolefin stocks (e.g., coroplast, Cor-X) without the addition of a catalyst.
POP+ offers superior opacity and high gloss while maintaining rapid cure rates ideal for in-line presses. POP+ provides a durable, non-blocking surface and demonstrates excellent outdoor durability. Halftones in this ink series are available in our unique, high-definition printing “New Rheology” viscosity.
Performance Properties:
- Outstanding adhesion to a wide variety of substrates
- No additives required for adhesion to Coroplast
- Low tack finish for easy handling of double-sided prints
- Good water resistance
- Flexible for multi-layer applications and die-cutting
- Suitable for exterior exposure to three (3) years on premium vinyl, 5 years with an overprint of Solar Shield Clear
Recommended Substrates:
POP+ exhibits excellent adhesion to pressure-sensitive vinyl, top-coated and print-treated polyester, polystyrene, ABS, polycarbonate, rigid vinyl, expanded foam PVC (Celtec), coated paper, board stocks, PETG, acrylic, high-density polyethylene, fluted polyolefins (coroplast, Cor-X), anodized aluminum, and some coated metals.
To determine the suitability of the product for the intended use, a pre-test prior to production is advised.
Curing:
POP+ will cure well when printed through 355 (140 cm) plain weave polyester mesh or finer. POP+’s optimal cure window of 125 to 175 mJ is generally achieved with one 200-watt per inch (80-watt per cm) mercury vapor lamp at belt speeds between 65-75 feet (19-23 meters) per minute.
Adhesion should be a minimum of 95% from the curing unit with final adhesion developing within four hours of initial polymerization. Coarser fabrics can be utilized; however, cure parameters may need to be adjusted for the increased ink film.
If a loss of gloss or adhesion due to insufficient cure is noticed, the use of 5 - 10% POP+ Mixing Clear will increase light penetration and improve cure.
Printing:
Mix well prior to every use. Although POP+ has been supplied in a press-ready condition, this system may be reduced by up to 10% with POP+ Thinner for special viscosity adjustments.
Care should be taken to print the ink at the optimal temperature of 70°-90°F (21°- 27°C). Cool ink will have heavier viscosity and will not flow properly, whereas excessively warm ink will be lower in viscosity, resulting in poor definition and decreased opacity.
Squeegee:
A 70 - 90 durometer polyurethane blade is recommended.
Coverage:
3200 to 3600 square feet per gallon for a film deposit of 0.40 to 0.60 mil.
Outdoor Use:
Extensive accelerated weathering tests indicate POP+ is suitable for outdoor exposure up to three years depending on substrate selection. The use of premium-grade, long-term vinyl films is recommended for decal applications intended to weather up to three years. Accelerated weathering is a reference standard and can’t precisely reproduce actual outdoor performance. Based on prior correlation of accelerated testing versus real-time exposure, 500 hours is equated to approximately one year, 45° south Florida. POP+ withstood 2,500 hours with a Solar Shield Clear Overprint and 1,500 hours without an overprint.
Metallics:
A superior two-part system comprised of POP+ Metallic Mixing Clear and the proper metallic paste has been developed. The increased viscosity of MMC helps ensure a good particle suspension, and our new metallic technology provides unparalleled premix shelf life and stability. The recommended mixing ratios are: 12% silver paste, 28% gold paste (by weight) to achieve the standard metallic colors. For optimum coverage and opacity, 280 - 305 (110 - 120 cm) plain weave monofilament mesh is recommended. Use POP+ Overprint Clear for extended weatherability and to improve the non-tarnishing properties of the product.
Storage:
Care should be taken to store ink in tightly closed containers located in a cool (60°F to 80°F / 15°C to 27°C), dark place. After long production runs, excess ink from the screen should be properly disposed of. With suitable conditions, the ink is expected to have a shelf life of approximately 12 months from the date of manufacture.
Precautions:
Read the material safety data sheet prior to processing. It contains instructions for precautions when processing, handling, and storing inks, as well as first aid. If ink comes in contact with skin, wipe ink off with a clean, dry cloth (do not use solvent). Wash and rinse the affected area with soap and water.
Process Printing:
For superior halftone reproduction, POP+ New Rheology halftones are available in three density levels. Additional control of densities may be achieved with the use of POP+ Halftone Extender Base. For best results, 380 (150 cm) plain weave mesh or finer and a smooth, thin stencil coating should be utilized with four-color process printing.
Press High Backlit Ready Density:
- POP+ Halftone Yellow: 0.90 / 1.10 / 1.35
- POP+ Halftone Magenta: 1.40 / 1.75 / 2.05
- POP+ Halftone Cyan: 1.40 / 1.80 / 2.20
- POP+ Halftone Black: 1.60 / 2.00 / 2.25
- POP+ Halftone Extender Base
Color Availability:
POP+ is available in twenty opaque standard colors. Custom matches, metallic, fluorescent, and transparent colors are obtainable upon request.
- POP+-101 Primrose Yellow
- POP+-210 Ultra Blue
- POP+-111 Lemon Yellow
- POP+-220 Emerald Green
- POP+-123 Medium Yellow
- POP+-225 Forest Green
- POP+-131 Brilliant Orange
- POP+-226 Lime Green
- POP+-135 Vivid Orange
- POP+-235 Teal
- POP+-141 Fire Red
- POP+-240 Purple
- POP+-151 Scarlet Red
- POP+-260 Brown
- POP+-155 Rubine Red
- POP+-301 Opaque Black
- POP+-160 Rhodamine Red
- POP+-311 Opaque White
- POP+-180 Warm Red
- POP+-312 Dense Black
- POP+-190 Process Blue
- POP+-026 Brilliant White
- POP+-200 Peacock Blue
- POP+ OP Overprint Clear
- POP+ MMC Metallic Mixing Clear
PANTONE® Matching System Colors:
The nine PANTONE® approved Color Matching System shades are used to simulate the PANTONE Color Specifier 1000 colors. Formulas were designed for maximum opacity and are available in book or Imaging Color Source software format.
- POP+-064 CMS GS Yellow
- POP+-066 CMS RS Yellow
- POP+-114 CMS Orange
- POP+-121 CMS YS Red
- POP+-164 CMS BS Red
- POP+-165 CMS Magenta
- POP+-127 CMS Violet
- POP+-230 CMS Blue
- POP+-325 CMS Green
- POP+ Tinting White
- POP+ Shading Black
- POP+ Mixing Clear
PANTONE® is a trademark of Pantone, Inc. Portions © Pantone, Inc., 1963, 1991.
Duraflex
Duraflex DF is a UV-curable ink system specifically formulated for flat, pressure-sensitive decal applications requiring exterior exposure for five years. Extensive weather tests have proven that Duraflex yields durable decals that will not curl at the edges due to ink/vinyl shrinkage or lose color intensity. Duraflex maintains a remarkably high gloss finish with minimal chalking after extended weathering. This ink has been formulated with lead-free, automotive-grade pigments, producing an extremely opaque, lightfast ink film.
Performance Properties:
- Suitable for five (5) years of exterior exposure
- Exceptional opacity and high gloss for vivid, long-life graphics
- Extremely flexible for multi-layer applications and die-cutting
- Low shrinkage, which diminishes edge curl on long-term vinyl
- Suitable with pre-mask films for easy application
- Solvent and abrasion-resistant for the most severe decal uses
- Non-blocking, low tack finish for easy handling
Recommended Substrates:
Duraflex adheres well to pressure-sensitive vinyl and print-treated polyester films. Duraflex has shown excellent adhesion to a wide variety of substrates and is more flexible than most multi-purpose UV ink systems. Additional substrates include: electrostatic vinyl, polycarbonate, PVC, some coated metals, vinyl-coated magnets, Polystyrene, and coated paper.
To determine the suitability of the product for the intended use, a pretest prior to production is advised. Five (5) year durability is contingent on the substrate with comparable exposure duration.
Curing:
Duraflex cures well with one 200-watt per inch lamp at belt speeds between 50-60 feet (20 meters) per minute using 355-390 (140-150cm) monofilament polyester mesh. A minimum of 175-200 mJ is required for complete cure.
Adhesion should be a minimum of 95% from the curing unit, with final adhesion developing within four hours of initial polymerization. Coarser fabrics can be utilized; however, cure parameters may need to be adjusted for the increased ink film.
If a loss of gloss or adhesion due to insufficient cure is noticed, the use of 5-10% DF Mixing Clear will increase light penetration and improve cure.
Printing:
Mix well prior to every use. Although DF has been supplied in a press-ready condition, this system may be reduced up to 10% with DF Thinner for special viscosity adjustments.
Care should be taken to print the ink at the optimal temperature of 70°F to 90°F (21°C to 27°C). Cool ink will have heavier viscosity and will not flow properly, whereas excessively warm ink will be lower in viscosity, resulting in poor definition and decreased opacity.
Squeegee:
A 70-90 durometer polyurethane blade is recommended.
Coverage: 3200 to 3600 square feet per gallon for a film deposit of 0.40 to 0.60 mil.
Outdoor Use: Extensive accelerated weathering tests have been completed on vinyl decals printed with Duraflex. The ink withstood 2500 hours of exposure with 4-hour cycle times of UV light and condensation at elevated temperatures with minimal color change and marginal shrinkage.
Accelerated machine weathering is reference standards and can’t precisely reproduce actual outdoor performance. Based on prior correlation of accelerated testing versus real-time exposure, 500 hours is equated to approximately one year, 45° south Florida.
The use of premium-grade, long-term vinyl films is recommended for all applications intended to weather three years or longer.
Pre-mask:
A medium to high tack adhesive is recommended for good adhesion.
Solar Shield Clear:
UV absorbers have been incorporated into the DF Solar Shield Overprint Clear, which lengthens the graphic's life by acting as a sunscreen. This clear requires more energy to cure than the normal Duraflex color range. A minimum of 225-250 mJ is needed.
Metallics:
A superior two-part system comprised of DF Metallic Mixing Clear and the proper metallic paste has been developed. The increased viscosity of MMC helps ensure a good particle suspension, and our new metallic technology allows unparalleled premix shelf life and stability. The recommended mixing ratios are: 12% silver paste, 28% gold paste (by weight) to achieve the standard metallic colors.
For optimum coverage and opacity, 280-305 (110-120 cm) plain weave monofilament mesh is recommended. Use DF Overprint Clear for extended weatherability and to improve the non-tarnishing properties of the product.
Storage:
Care should be taken to store ink in tightly closed containers located in a cool (60°F to 80°F / 15°C to 27°C), dark place. After long production runs, excess ink from the screen should be properly disposed. With suitable conditions, the ink is expected to have a shelf life of approximately 12 months from the date of manufacture.
Precautions:
Read the material safety data sheet prior to processing. It contains instructions for precautions when processing, handling, and storing inks, as well as first aid. If ink comes in contact with the skin, wipe ink off with a clean, dry cloth (do not use solvent). Wash and rinse the affected area with soap and water.
Process Printing:
Duraflex halftones are available in three density levels. Additional control of densities may be achieved with the use of DF Halftone Extender Base. For best results, 355 (140 cm) plain weave mesh or finer and a smooth, thin stencil coating should be utilized with four-color process printing.
- Press
- High
- Backlit
- Ready Density
- DF Halftone Yellow: 0.90, 1.10, 1.35
- DF Halftone Magenta: 1.40, 1.75, 2.05
- DF Halftone Cyan: 1.40, 1.80, 2.20
- DF Halftone Black: 1.60, 2.00, 2.25
- DF Halftone Extender Base
Color Durability:
Duraflex DF is available in twenty opaque standard colors. Custom matches, metallic, fluorescent, and transparent colors are obtainable upon request.
- DF-101 Primrose Yellow
- DF-210 Ultra Blue
- DF-111 Lemon Yellow
- DF-220 Emerald Green
- DF-123 Medium Yellow
- DF-225 Forest Green
- DF-131 Brilliant Orange
- DF-226 Lime Green
- DF-135 Vivid Orange
- DF-235 Teal
- DF-141 Fire Red
- DF-240 Purple
- DF-151 Scarlet Red
- DF-260 Brown
- DF-155 Rubine Red
- DF-301 Opaque Black
- DF-160 Rhodamine Red
- DF-311 Opaque White
- DF-180 Warm Red
- DF-312 Dense Black
- DF-190 Process Blue
- DF-026 Brilliant White
- DF-200 Peacock Blue
- DF Overprint Clear
- DF-205 Reflex Blue
- DF Metallic Mixing Clear
PANTONEⓇ Matching System: The nine ⓇPANTONE approved Color Matching System shades are used to simulate the PANTONE Color Specifier 1000 colors. Formulas were designed for maximum opacity.
GBS UV Container Ink
Gloss Bottle GBS is a one-part screen ink developed with the needs of the container printer in mind. This is the only UV ink series with adhesion to plastics including HDPE, LDPE, PET, PVC, and PP without the use of adhesion promoters or catalysts. The ink exhibits excellent flexibility for squeeze tests on thin-walled LDPE, yet it maintains a durable chemical and water-resistant surface which withstands the most stringent product tests. The unique rheological properties of GBS present smooth printability with minimized drip-through and reduced cleanup time.
The GBS Series is offered with an unmatched blending system. All colors used in the NSC’s Color Matching System (CMS) are 20% stronger than current industry standards. This high-density system provides the most vibrant, opaque colors and allows the printer to use higher mesh counts to reduce ink usage thereby saving money.
Performance Properties:
• Unequaled, straight from the can adhesion to poly containers
• Does not require flame treatment for PET or PVC adhesion
• Highly flexible for thin-walled containers
• Superb water and full chemical resistance after 24 hours
• Fast, tack-free cure for running high line speeds
• 20% stronger CMS colors for vibrant, sharp hues
Recommended Substrates:
GBS Series exhibits excellent adhesion to a wide range of container materials. For best results the following require a flame treatment prior to printing: high-density polyethylene, low-density polyethylene, and polypropylene. No flame is required for PVC and PET bottles. To determine suitability of the product for the intended use, a pretest prior to production is advised.
Curing:
GBS will cure well when printed through 305-380 (120-150cm) plain weave polyester mesh. A minimum of 125 mJ is required to cure standard colors. This optimal cure window is generally achieved with one 300 watt per inch mercury vapor lamp at press speeds up to 70 containers per minute.
Adhesion should be a minimum of 95% from the curing unit with final adhesion developing within four hours of initial polymerization.
If a loss of gloss or adhesion due to insufficient cure is noticed, the use of 5-10% GBS Mixing Clear will increase light penetration and improve cure in opaque colors. Mix 5-10% GBS Overprint Clear with white inks to increase cure rate.
Printing:
Mix well prior to every use. Although GBS has been supplied in press-ready condition, this system may be reduced up to 10% with GBS Thinner for special viscosity adjustments.
Care should be taken to print the ink at the optimal temperature of 70°-90°F (21°- 27°C). Cool ink will have heavier viscosity and will not flow properly whereas excessively warm ink will be lower in viscosity resulting in poor definition and decreased opacity.
Squeegee:
70-90 durometer polyurethane blade is recommended.
Coverage:
3200 to 3600 square feet per gallon for film deposit of .40 to .60 mil.
Chemical Resistance:
To be announced.
Water Resistance:
GBS has passed all laboratory-conducted water immersion/wet flex tests. Printed bottles were tested immediately as well as after a 24-hour ‘post cure’ period. This period, between curing and testing, provides the ink film and substrate time to stabilize, improving adhesion properties.
Metallics:
A superior two-part system comprised of GBS Metallic Mixing Clear and the proper metallic paste has been developed. The increased viscosity of MMC helps ensure a good particle suspension and our new metallic technology provides unparalleled premix shelf life and stability. The recommended mixing ratios are: 12% silver paste, 28% gold paste (by weight) to achieve the standard metallic colors.
For optimum coverage and opacity, 280-305 (110 – 120cm) plain weave monofilament mesh is recommended. When overprinting metallic inks, best results are achieved with the addition of 5% 1534 Adhesion Promoter.
Storage:
Care should be taken to store ink in tightly closed containers located in a cool (60 degrees F to 80 degrees F(15 degrees to 27 degrees), dark place. After long production runs excess ink from the screen should be properly disposed. With suitable conditions, the ink is expected to have a shelf life of approximately 12 months from the date of manufacture.
Precautions:
Read the material safety data sheet prior to processing. It contains instructions for precautions when processing, handling, and storing inks, as well as first aid. If ink comes in contact with skin, wipe ink off with a clean, dry cloth (do not use solvent). Wash and rinse the affected area with soap and water.
Process Printing:
For superior halftone reproduction, Gloss Bottle New Rheology halftones are available. Additional control of densities may be achieved with the use of GBS Halftone Extender Base. For best results, 355 (140 cm) plain weave mesh or finer and a smooth, thin stencil coating should be utilized with four-color process printing.
- GBS Halftone Yellow 1.10
- GBS Halftone Magenta 1.75
- GBS Halftone Cyan 1.80
- GBS Halftone Black 2.00
- GBS Halftone Extender Base
Color Availability:
Gloss Bottle is available in eight standard opaque colors. Metallic and fluorescent colors are readily available, in addition to custom color matches formulated to your specific criteria.
- GBS-111 Lemon Yellow
- GBS-301 Opaque Black
- GBS-131 Brilliant Orange
- GBS-311 Opaque White
- GBS-141 Fire Red
- GBS-312 Dense Black
- GBS-155 Rubine Red
- GBS-026 Brilliant White
- GBS-160 Rhodamine Red
- GBS-205 Reflex Blue
- GBS-210 Ultra Blue
- GBS-220 Emerald Green
High Density Matching System Colors:
The nine High Density Color Matching System shades are used to simulate the PANTONE Color Specifier 1000 colors. Formulas were designed for maximum opacity and are available in book or Imaging Color Source software format.
- GBS-064HD CMS GS Yellow
- GBS-230HD CMS Blue
- GBS-066HD CMS RS Yellow
- GBS-114HD CMS Orange
- GBS-121HD CMS YS Red
- GBS-325HD CMS Green
- GBS-164HD CMS BS Red
- GBS-TWTinting White
- GBS-165HD CMS Magenta
- GBS-HDMixing White HD
- GBS-127HD CMS Violet
- GBS-SBShading Black
- GBS-MX Mixing Clear
Color Availability:
Gloss Bottle is available in eight standard opaque colors. Metallic and fluorescent colors are readily available, in addition to custom color matches formulated to your specific criteria.
- GBS-111 Lemon Yellow
- GBS-301 Opaque Black
- GBS-131 Brilliant Orange
- GBS-311 Opaque White
- GBS-141 Fire Red
- GBS-312 Dense Black
- GBS-155 Rubine Red
- GBS-026 Brilliant White
- GBS-160 Rhodamine Red
- GBS-OP Overprint Clear
- GBS-205 Reflex Blue
- GBS-MMC Metallic Mixing Clear
- GBS-210 Ultra Blue
- GBS-220 Emerald Green
- High Density Matching System Colors: The nine High Density Color Matching System shades are used to simulate the PANTONE Color Specifier 1000 colors. Formulas were designed for maximum opacity and are available in book or Imaging Color Source software format.
- GBS-064HD CMS GS Yellow
- GBS-230HD CMS Blue
- GBS-066HD CMS RS Yellow
- GBS-114HD CMS Orange
- GBS-121HD CMS YS Red
- GBS-325HD CMS Green
- GBS-164HD CMS BS Red
- GBS-TWTinting White
- GBS-165HD CMS Magenta
- GBS-HDMixing White HD
- GBS-127HD CMS Violet
- GBS-SBShading Black
- GBS-MX Mixing Clear
WR Multi-Purpose Banner Ink
WR is distinct in its ability to offer non-blocking, flexibility needed for banner applications while also providing adhesion to nearly all point-of-purchase stocks. This provides screen printers with the opportunity to reduce ink inventory by stocking a single ink line. Custom colors can also be duplicated easily on various stocks.
Unlike other multipurpose inks, Ultrabond’s exceptional flexibility and adhesion stand up to the demand of the most stringent finishing requirements. Ultrabond provides a durable, non-blocking surface and has excellent outdoor durability.
Performance Properties:
• Broadcast adhesion range of any NUVS UV ink
• Flexible for sewing, grommeting, and die-cutting without cracking
• Allows durable face printing without re-wetting or picking
• Low tack finish to eliminate slip-sheeting
• Water and abrasion-resistant
• Superior opacity provides better color trapping
• N-VP Free
Recommended Substrates:
Excellent adhesion to vinyl banners, electrostatic vinyl, and polyethylene banner material having treatment levels of at least 40 dynes. Ultrabond also provides excellent adhesion to ABC, Acrylic, Cardstock, Expanded PVC, Print Treated Polyester, Coated/Uncoated Paper, PETG, treated HDPE, Polycarbonate, Fluted Polyolefins, Treated Polypropylene, Polystyrene, Tyvek, Pressure Sensitive Vinyl, Unsupported Vinyl, and Low Tack Vinyl. Ultrabond has also shown good adhesion to coated metals.
To determine suitability of the product for the intended use, a pretest prior to production is advised. Our recommendations are based on present knowledge. Due to the limited life of surface treatments on polypropylene banner (Propaque) and fluted polyolefin materials (Coroplast), testing is required prior to production.
Curing:
Ultrabond will cure well when printed through 355 (140 cm) plain weave polyester mesh or finer. A minimum of 125-160 mJ’s are required to cure standard WR colors and banner stocks. This optimal cure window is generally achieved with one 200-watt per inch mercury vapor lamp at belt speeds between 75-100 feet (20-30 meters) per minute. Heavier gauge stocks and dark colors, which may act as a heat sink, may require 200 mJ’s or more.
Adhesion should be a minimum of 95% from the curing unit with final adhesion developing within four hours of initial polymerization. Coarser fabrics can be utilized; however, cure parameters may need to be adjusted for the increased ink film.
If a loss of gloss or adhesion due to insufficient cure is noticed, the use of 5-10% WR Mixing Clear will increase light penetration and improve cure. Additions of Thinner will not improve cure and may cause the rate of decrease
Printing:
Mix well prior to every use. Although WR has been supplied in press-ready condition, this system may be reduced up to 10% with WR Thinner for special viscosity adjustments.
Care should be taken to print the ink at the optimal temperature of 70°-90° F (21°- 27°C). Cool ink will have heavier viscosity and will not flow properly whereas excessively warm ink will be lower in viscosity resulting in poor definition and decreased opacity.
Squeegee:
70 - 90 durometer polyurethane blade is recommended.
Coverage:
3600 to 3800 square feet per gallon for film deposit of .40 to .60 mil.
Outdoor Use:
Extensive accelerated weathering tests have been completed on vinyl printed with Ultrabond, with an Overprint Clear. The ink withstood 1,500 hours of exposure with 4-hour cycle times of UV light and condensation at elevated temperatures with minimal color change and marginal shrinkage.
Accelerated machine weathering are reference standards and can’t precisely reproduce actual outdoor performance. Based on prior correlation of accelerated testing versus real-time exposure, 1,500 hours is equated to approximately three years, 45° south Florida.
Metallics: A superior two-part system comprised of WR Metallic Mixing Clear and the proper metallic paste has been developed. The increased viscosity of MMC helps insure a good particle suspension and our new metallic technology provides unparalleled premix shelf life and stability. The recommended mixing ratios are: 12% silver paste, 28% gold paste (by weight) to achieve the standard metallic colors.
For optimum coverage and opacity, 280 - 305 (110 - 120 cm) plain weave monofilament mesh is recommended. Use WR Overprint Clear for extended weatherability and to improve the non-tarnishing properties of the product.
Storage:
Care should be taken to store ink in tightly closed containers located in a cool (6°F to 8°F / 15° to 27°C), dark place. After long production runs, excess ink from the screen should be properly disposed. With suitable conditions, the ink is expected to have a shelf life of approximately 12 months from the date of manufacture.
Precautions:
Read the material safety data sheet prior to processing. It contains instructions for precautions when processing, handling, and storing inks, as well as first aid. If ink comes in contact with skin, wipe ink off with a clean, dry cloth (do not use solvent). Wash and rinse the affected area with soap and water.
Process Printing: For superior halftone reproduction, Ultrabond halftones are available in three density levels. Additional control of densities may be achieved with the use of WR Halftone Extender Base. For best results, 380 (150 cm) plain weave mesh or finer and a smooth, thin stencil coating should be utilized with four-color process printing.
- Press High Backlit
- Ready Density Density
- WR Halftone Yellow .90 1.10 1.35
- WR Halftone Magenta 1.40 1.75 2.05
- WR Halftone Cyan 1.40 1.80 2.20
- WR Halftone Black 1.60 2.00 2.25
- WR Halftone Extender Base
Color Availability:
Ultrabond WR is available in opaque standard colors. Custom matches, metallic, fluorescent, and transparent colors are obtainable upon request.
- WR-111 Lemon Yellow WR-210 Ultra Blue
- WR-123 Medium Yellow WR-220 Emerald Green
- WR-131 Brilliant Orange WR-301 Opaque Black
- WR-141 Fire Red WR-311 Opaque White
- WR-151 Scarlet Red WR-312 Dense Black
- WR-155 RWRine Red WR-026 Brilliant White
- WR-160 Rhodamine Red WR Overprint Clear
- WR-180 Warm Red WR Metallic Mixing Clear
- WR-190 Process Blue WR Backing White
- WR-200 Peacock Blue WR Barrier White
- WR-205 Reflex Blue
PANTONE® Matching System Colors:
The nine PANTONE® approved Color Matching System shades are used to simulate the PANTONE Color Specifier 1000 colors. Formulas were designed for maximum opacity and are available in book or imaging Color Source software format.
- WR-064 CMS GS Yellow
- WR-066 CMS RS Yellow
- WR-114 CMS Orange
- WR-121 CMS YS Red
- WR-164 CMS BS Red
- WR-165 CMS Magenta
- WR-127 CMS Violet
- WR-230 CMS Blue
- WR-325 CMS Green
- WR Tinting White
- WR Shading Black
- WR Mixing Clear
PANTONE® is a trademark of Pantone, Inc. Portions © Pantone, Inc., 1963, 1991.
Thermoform (TF) Vacuum Formable
Thermoform TF is an extremely flexible ultraviolet curable screen printing ink specifically formulated for printing plastics used in vacuum forming.
Thermoform exhibits outstanding vacuum forming characteristics and ink lengthening while maintaining excellent adhesion and opacity. Additionally, this ink provides ideal characteristics for heat bending and routing acrylic sheets with no chipping or loss of adhesion.
Performance Properties:
• Extreme elongation for maximized draw depth, exceeding 6” (15 cm)
• Multiple passes can be heat bent and routed without chipping
• Excellent intercoat adhesion, even when cured multiple times
• Contains lightfast, lead-free pigments
• Extreme moisture resistance for exterior exposures
• Elevated halftone color strength for back-lit applications
Recommended Substrates:
ThermoForm TF was designed to adhere to plastics used for vacuum forming, including, but not limited to: polystyrene, PETG, polycarbonate, high impact styrene, and PVC. TF also has excellent adhesion to acrylics (Plexiglass®).
To determine suitability of the product for the intended use, a pretest for proper adhesion prior to production is advised.
Curing:
Thermoform cures well when printed through 355 (140 cm) plain weave Polyester mesh or finer. TF’s optimal cure window of 310 to 350 mJ is generally achieved with one 300 watt per inch lamp at a belt speed of 30 feet (10 meters) per minute. This should provide a thorough cure of the product including opaque colors. Belt speeds can be increased dramatically as the substrate gauge is reduced. Thick, plastic substrates act as a heat sink and decrease cure rates.
For maximum opacity retention on deep draws, coarser screen mesh may be used, increase mJ output and test for proper cure and adhesion. Excessive film thickness does not impede vacuum forming properties.
Adhesion should be a minimum of 90% from the curing unit with final adhesion developing within four hours of initial polymerization. Coarser fabrics can be utilized; however, cure parameters may need to be adjusted for the increased ink film.
If a loss of gloss or adhesion due to insufficient cure is noticed, the use of 5-10% TF Mixing Clear will increase light penetration and improve cure.
Printing:
Mix well prior to every use. Although TF has been supplied in press-ready condition, this system may be reduced up to 10% with TF Thinner for special viscosity adjustments.
Care should be taken to print the ink at the optimal temperature of 70°-90°F (21°- 27°C). Cool ink will have heavier viscosity and will not flow properly whereas excessively warm ink will be lower in viscosity resulting in poor definition and decreased opacity.
Squeegee:
70 - 90 durometer polyurethane blade is recommended.
Coverage:
3200 to 3600 square feet per gallon for film deposit of .40 to .60 mil.
Outdoor Use:
Extensive accelerated weathering tests have been completed. The ink withstood over 500 hours of exposure with 4-hour cycle times of UV light and condensation at elevated temperature. Accelerated machine weathering are reference standards and can’t precisely reproduce actual outdoor performance. Based on prior correlation of accelerated testing versus real-time exposure, 500 hours is equated to approximately one year, 45° south Florida.
Metallics:
A superior two-part system comprised of TF Metallic Mixing Clear and the proper metallic paste has been developed. The increased viscosity of MMC helps insure a good particle suspension and our new metallic technology provides unparalleled premix shelf life and stability. The recommended mixing ratios are: 12% silver paste, 28% gold paste (by weight) to achieve the standard metallic colors.
For optimum coverage and opacity, 280 - 305 (110 - 120 cm) plain weave monofilament mesh is recommended. Use TF Overprint Clear for extended weatherability and to improve the non-tarnishing properties of the product.
Storage:
Care should be taken to store ink in tightly closed containers located in a cool (60°F to 80°F / 15° to 27°C), dark place. After long production runs, excess ink from the screen should be properly disposed. With suitable conditions, the ink is expected to have a shelf life of approximately 12 months from the date of manufacture.
Precautions:
Read the material safety data sheet prior to processing. It contains instructions for precautions when processing, handling, and storing inks, as well as first aid. If ink comes in contact with skin, wipe ink off with a clean, dry cloth (do not use solvent). Wash and rinse the affected area with soap and water.
Process Printing:
For superior halftone reproduction, Thermoform New Rheology halftones are available in two density levels. Additional control of densities may be achieved with the use of TF Halftone Extender Base. For best results, 355 (140 cm) plain weave mesh or finer and a smooth, thin stencil coating should be utilized with four-color process printing.
- TF Halftone Yellow 1.10 1.35
- TF Halftone Magenta 1.75 2.05
- TF Halftone Cyan 1.80 2.20
- TF Halftone Black 2.00 2.25
- TF Halftone Extender Base
Color Availability: Thermoform TF is available in twenty opaque standard colors. Custom matches, metallic, fluorescent, and transparent colors are obtainable upon request.
- TF-111 Lemon Yellow TF-220 Emerald Green
- TF-123 Medium Yellow TF-225 Forest Green
- TF-131 Brilliant Orange TF-226 Lime Green
- TF-135 Vivid Orange TF-235 Teal
- TF-141 Fire Red TF-240 Purple
- TF-151 Scarlet Red TF-260 Brown
- TF-155 Rubine Red TF-301 Opaque Black
- TF-160 Rhodamine Red TF-311 Opaque White
- TF-180 Warm Red TF-312 Dense Black
- TF-190 Process Blue TF Barrier White
- TF-200 Peacock Blue TF Overprint Clear
- TF-205 Reflex Blue TF Metallic Mixing Clear
- TF-210 Ultra Blue
PANTONE® Matching System Colors:
The nine PANTONE® approved Color Matching System shades are used to simulate the PANTONE Color Specifier 1000 colors. Formulas were designed for maximum opacity and are available in book or Imaging Color Source software format.
- TF-064 CMS GS Yellow
- TF-066 CMS RS Yellow
- TF-114 CMS Orange
- TF-121 CMS YS Red
- TF-164 CMS BS Red
- TF-165 CMS Magenta
- TF-127 CMS Violet
- TF-230 CMS Blue
- TF-325 CMS Green
- TF Tinting White
- TF Shading Black
- TF Mixing Clear
PANTONE® is a trademark of Pantone, Inc. Portions © Pantone, Inc., 1963, 1991.
Title or Question
Describe the item or answer the question so that site visitors who are interested get more information. You can emphasize this text with bullets, italics or bold, and add links.Button
Textile Screen Printing Inks
What is Discharge Ink?
Discharge screen printing is very popular in today's market. This ink can be printed as direct discharge, dye discharge, or used as an under base for water-based or plastisol inks. Discharge water-based ink produces an extremely soft hand and gives the garment a unique vintage look customers love!
What pigments do they offer?
Jantex offers a range of pigments tailored to different printing needs:
Jantex Standard Pigments:
This standard line of pigments is designed for water-based printing systems, boasting over 15 colors for versatile color matching. Recommended ink loads should not exceed 8-10% of combined pigments.
Jantex Concentrated Pigments:
For more vibrant colors without diluting your base, Jantex offers a concentrated line of pigments suitable for water-based printing systems, including discharge printing. With over 12 colors available, this line provides ample color matching possibilities. Recommended ink loads should not exceed 5-6% of combined pigments.
Jantex RFU Colors:
These Ready For Use water-based printing inks are pre-mixed and ready to go. The standard RFU color line maintains a 10% color to base ratio, ensuring rich, vibrant colors that can be easily adjusted by basing back for lighter shades.
Custom Color Matching:
If you need a specific color matched, including PMS colors, Jantex offers a color matching service for a small fee. Simply provide a swatch or wet sample of the color, along with details about the substrate and printing job. Jantex will handle the rest. Please note that this service is not available for discharge printing. Contact us for pricing and turnaround time.
Downloadable Color Card Coming Soon:
Stay tuned for a downloadable color card to explore Jantex's color offerings in detail.
WM Plastics
10-9521 Brite White
Introducing Brite White, quite possibly the last white ink you'll ever need. Offering the pinnacle of soft, smooth texture, Brite White boasts unparalleled printability, setting a new industry standard. This ink provides exceptional coverage, smoothness, and a soft hand for white underlays, ensuring brighter colors on top. And with its Low Bleed Formula, Brite White meets all your requirements for a dependable white ink.
Features:
- Smooth Body
- Great Coverage
- Low Bleed
- Soft Hand
- Bright Colors on an Underlay
- Brightest White
Printing Instructions:
Best results with medium squeegees and optimal mesh tensions. Low mesh tensions can hinder clearing, affect registration, and coverage.
Use more upright squeegee angles to print with the edge of the blade, not the side. A softer squeegee or tilting it to the side may improve coverage but might affect the final print's "hand" and registration, depending on the design.
If ink doesn't clear well, adjust ink viscosity with curable reducer, increase squeegee pressure, decrease speed, tilt squeegee more upright, or increase off-contact. A combination of these changes may be necessary.
Technical Details:
- Substrates: Cotton, Poly/Cotton Blends, and Acrylics
- Bleed Resistance: Good
- Opacity: High
- Mesh: 87 to 300
- Screen Tension: 20 newton or higher
- Stencil: Direct, Indirect & Capillary
- Squeegee Type: 70, 70/90, 70/90/70
- Squeegee Blade: Sharp
- Squeegee Angle: 45 degrees
- Squeegee Speed: Average
- Pressure: Average to light
- Flashing: Fast (700 F for 4 seconds). Flash times depend on mesh.
- Gel Temp: 157
- Cure Temp: 1 to 1 ½ minutes at 325 F
Reducer: 10-9906 Curable Reducer
Caution:
Always test this product for curing, adhesion, crocking, opacity, washability, and other requirements in your specific application before using in production.
Storage:
Ideally at 80 F. Keep out of direct sunlight and heat.
Wash-up:
Any Plastisol Screen wash or Mineral Spirits.
10-2195 Majestic Black
Introducing a premium black ink, highly favored by automatic printers for its easy flow and multipurpose versatility, suitable for any head station. This ink is renowned for its exceptional wet-on-wet printing capabilities without any buildup, delivering a soft hand when printed.
Features:
- Smooth Body
- Great Coverage
- Soft Hand
- No Buildup
- Clears Screen well
Printing Instructions:
When flooding, use minimal pressure.
Ensure proper pressure and angle of the squeegee when pulling with constant speed.
Increasing the number of squeegee strokes can enhance deposit.
Heavy deposits may lead to increased dot gain and smuggling.
Technical Details:
- Substrates: Cotton, Poly/Cotton Blends, and Acrylics
- Bleed Resistance: None
- Opacity: High
- Mesh: 86 to 300
- Screen Tension: 20 newton or higher
- Stencil: Direct, Indirect & Capillary
- Squeegee Type: 70, 70/90, 70/90/70
- Squeegee Blade: Sharp
- Squeegee Angle: 45 degrees
- Squeegee Speed: Normal
- Pressure: Average
- Flashing: Slow (700 F for 9 seconds). Flash times vary based on mesh.
- Gel Temp: 185 F
- Cure Temp: 1 to 1 ½ minutes at 325 F
- Thinning: 10-9906 Curable Reducer
Caution:
Always test this product for curing, adhesion, crocking, opacity, washability, and other requirements in your specific application before using in production.
Storage:
Ideally at 80 F. Keep out of direct sunlight and heat.
Wash-up:
Any Plastisol Screen wash or Mineral Spirits.
UV DRYERS & PARTS
UV DRYERS
Our UV dryer technology represents a groundbreaking advancement in UV drying. It introduces a revolutionary high-energy, low-heat system designed to ensure the effective curing of all UV clear and pigmented coatings. Featuring our patent-pending reflector, our system enables a more efficient air-cooling mechanism that dissipates heat from both sides of the reflector, maintaining a consistently low temperature throughout the curing unit.
Full Description
With its accelerated high-speed curing capability, our technology can now instantly cure UV inks on even the most heat-sensitive stocks while minimizing heat build-up, often requiring only a single lamp for most applications. Our conveyorized system boasts a true vacuum substrate hold-down, enabling higher production rates without worrying about substrate flutter. Individual lamp output control allows for curing at 200, 300, and even 400 watts per linear inch, catering to a wide range of substrates including paper, cardboard, vinyl, and plastics.
Our dryers are available in standard widths of 12, 18, 24, 30, 36, 42, 48, 55, and 60 inches. The feed-in and run-out conveyor lengths can be customized to meet your specific requirements. Equipped with built-in safety interlocks at all openings, our dryers ensure instant power shut-off if lifted, preventing accidental operator exposure to the UV light source.
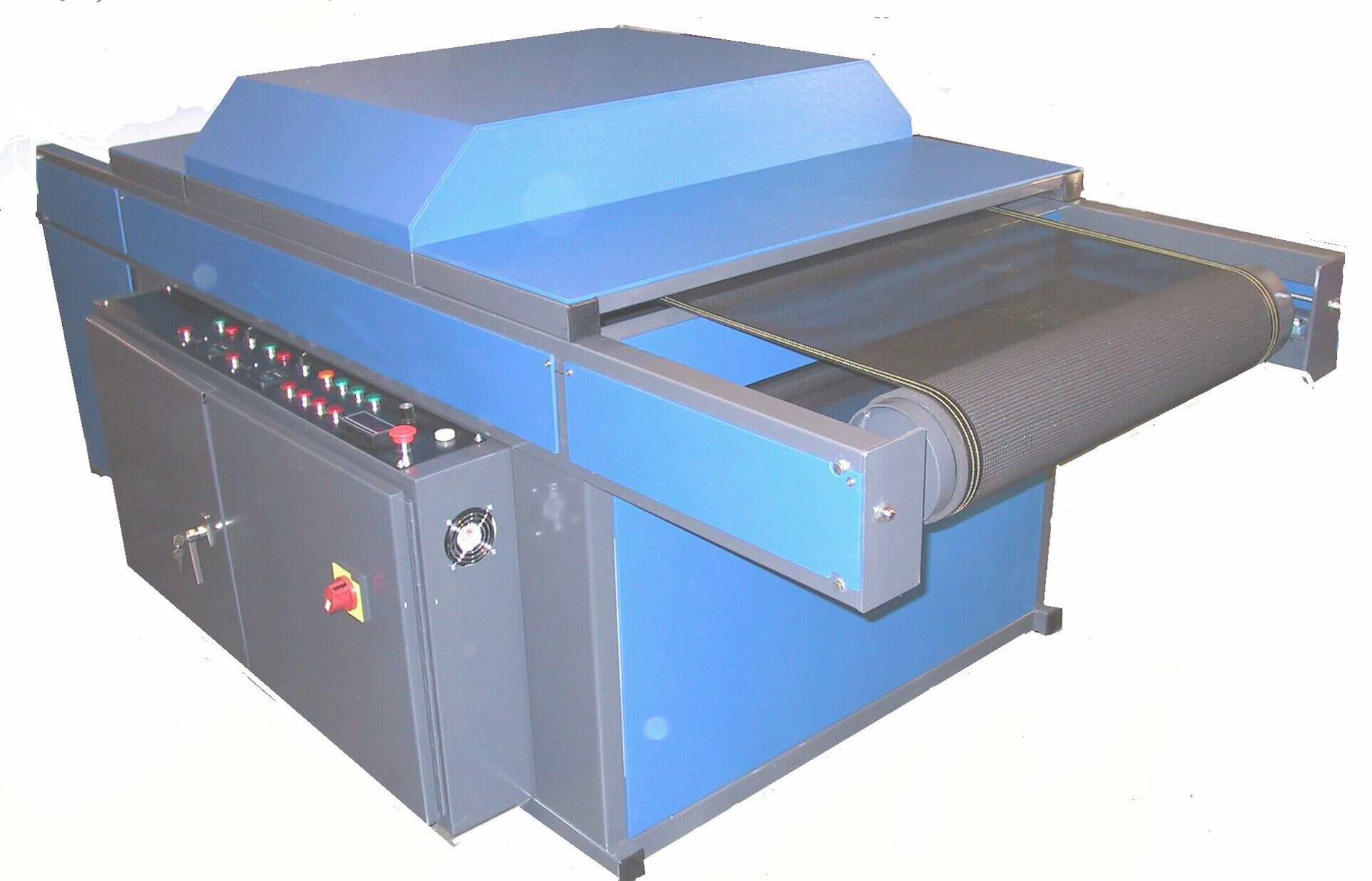
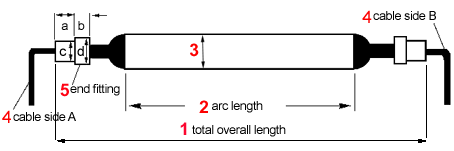
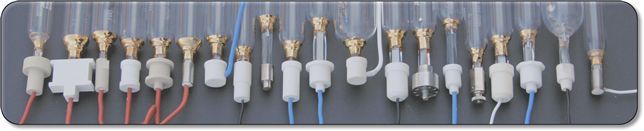
REPLACEMENT UV LAMPS
We offer a comprehensive range of UV Curing (Mercury Vapor) and Exposure (Metal Halide) lamps. With our extensive purchasing capabilities, we strive to provide competitive pricing on every lamp we sell. Whether you need an exact match or a suitable alternative, we've got you covered.
Full Description
Here are a number of equipment manufacturers whose UV curing and exposure lamps we sell. If your equipment is not listed, please contact us for availability and pricing. The easiest way to determine the lamp replacement is by answering the following questions.
- AAA
- AWT
- FMA
- SPE
- TAS
- Aetek
- Advance American
- American Screen Printing
- American UV
- Anatol
- Argon
- Fusion
- Olec
- OnLine Energy
- ORC
- Phillips
- Precision
- Prime UV
- SIAS
- Svecia
- TAS
- Theimer
- Ushio
- Uvex/Dynachem
REPLACEMENT CONVEYOR BELTS
Open mesh Teflon® PTFE-impregnated fiberglass belting is available in brown or with a black U.V. block coating in widths up to 118" and any length. The fluorocarbon resins used in the curing process are chemically inert, and the woven glass substrate provides exceptional strength and dimensional stability. Its non-stick surface, operating temperature range from -100°F to +550°F, and the 70% open area make this belting the perfect solution for multiple applications.
Full Description
Standard Features:
- Double Sewn Edges
- Solvent Resistant
- Excellent Tracking
- Lightweight Construction
- Standard Alligator Lacing
- High-Quality Edge Reinforcements
- Industry's Heaviest Teflon Coating for Handling Sharp Materials
- Temperature Resistance Up to 500°F (287°C)
- All Belts come with 5 mm Tear and Crease Resistant Edges
How to Measure Coated Fiberglass Belts:
There are three ways to quickly and effectively measure the length of the belt you need. It is important to get it right, since these belts are custom-made and often cannot be lengthened. They can sometimes be shortened, but that’s an expensive proposition that can be avoided if a little time and the proper technique are applied when taking measurements.
Option 1:
The simplest way to measure a belt is to take the old one off of the machine, lay it on the floor, and measure it. Of course, this is seldom an option, as a machine needs to run to make money for the company. Additionally, removing a belt that is operating may not be advisable since putting it back on and getting it to track correctly can be difficult.
If the machine needs to continue to produce, proceed to Option II.
Option 2:
Another very easy way to measure your belt is to simply take a non-stretching material (a good quality wire rope, string, metal tape, etc.) and loop it around the belt or, in the case of a mesh belt, tie it off and make one revolution. Then measure the string, and you’ve got your belt length.
IMPORTANT: Take note of your pulley locations. Be certain to consider the location of your take-up pulleys to allow for future adjustment.
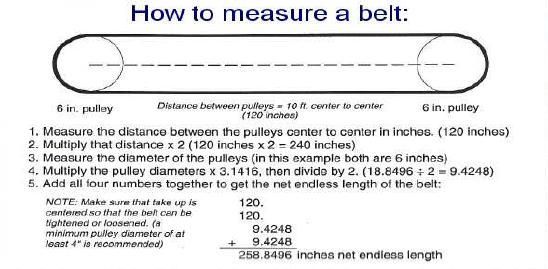
SCREEN PRINTING FILM
Screen Printing Waterproof Film is sold by the roll to reduce the cost of your films. Screen printers need to have high-quality film to produce a quality print job and maintain consistent printing.
FREE SHIPPING ON ALL WATERPROOF FILM
- 14" Roll: $72.23 each
- 17" Roll: $111.87 each
- 24" Roll: $126.17 each
- 36" Roll: $165.64 each
- 44" Roll: $243.25 each
OUR MISCELLANEOUS EQUIPMENT
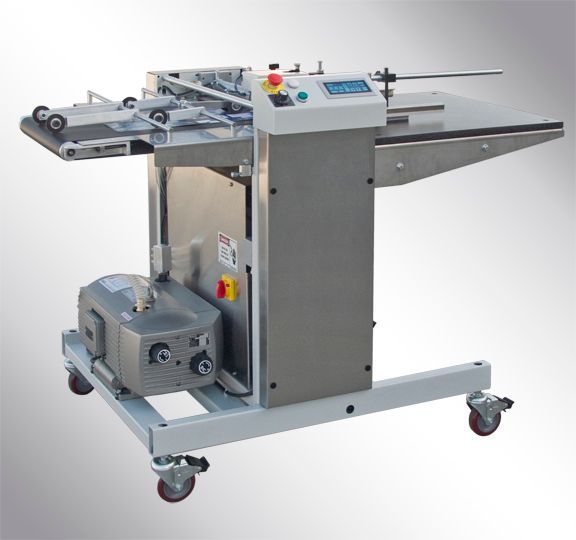
DEEP PILE FEEDER
The FMA deep pile Feeder is available in three sizes: 16" x 31", 20" x 31", and 24" x 31". Equipped with a vacuum wheel feed, it boasts a touch screen control panel for user-friendly operation. Features include auto start and shut down, a sheet counter, and a countdown feature for enhanced productivity. Additionally, it offers an auto jog function, adjustable vacuum time, and sheet gap settings for customization. Floating side guides ensure accurate alignment, while its capacity accommodates materials up to approximately 24" in size. With fast and slow adjustment options, it provides versatility for various applications.
BAUM DEEP PILE FEEDER
The Baum Deep Pile Feeder offers impressive specifications, with a maximum sheet width of 20.50" and length of 33.00", accommodating a maximum pile height of 25". It operates at a maximum feeding speed of 8000 ipm using a rotary vacuum wheel feeding device. Designed for efficiency, it operates on 220 volts, single-phase, 50/60 hertz, drawing 20 amps. Equipped with heavy-duty casters for mobility, it features a double sheet detector and a one-sheet test mode for precision. Additionally, it includes a total counter with reset functionality, along with a batch counter with an interrupt feature for batch counting and stopping purposes.
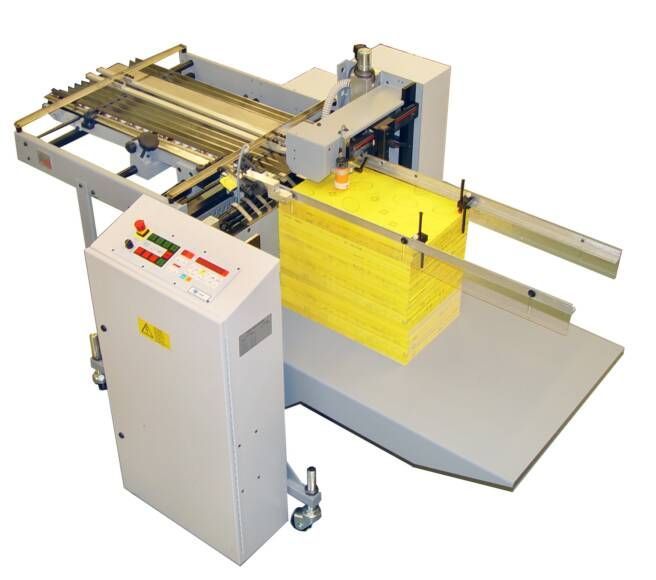
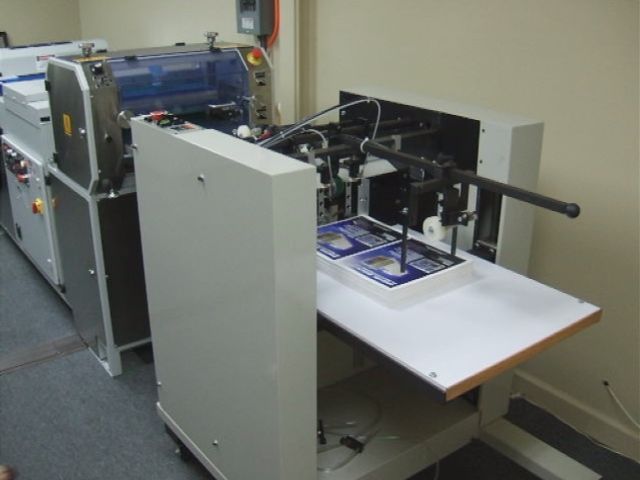
VACUUM CUP FEEDER
Our feeders have a size range of 8"x8" up to 28"x40", accommodating 6-point to 15-point stock. Running speeds can reach up to 5,000 sheets per hour, depending on stock and conditions, with a pile capacity of 23". Becker pumps supply the vacuum and air. Standard sizes include 15"x20", 20"x30", and 28"x40", but we offer customization to meet your specifications. Key features include vacuum suction cups, standard double sheet detection, simple and fast setup, variable feed speeds, and supplemental air for enhanced performance.
ISG Ascending Pile Stacker
The stacker streamlines operations for high-volume jobs by automating the line, eliminating the need for manual hand loading from a drop box. This enhancement significantly reduces labor demands, allowing personnel to focus on other tasks and increasing overall efficiency. By automating the stacking process, the system optimizes workflow and throughput, enabling smoother and more productive operations.
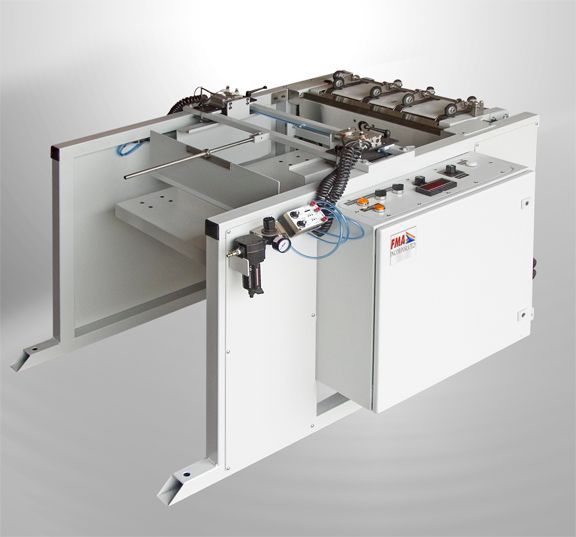
CREASE MASTER PLUS
The CreaseMaster Plus is ideal for mid- to high-volume users, ensuring a professional finish for every job. This pneumatic model is available in two production speeds: 3600 sph or 4600 sph, both offering multiple creases per sheet, job memory, as well as optional strike perf. The system incorporates a user-friendly touch screen, allowing for easy operation.
Features
Electrical: 120V/230V, 60/50Hz, 5.0 Amp
Maximum Speed (impact creasing): 3600 8.5 x 11" sheets per hour
Maximum Speed (rotary perf/score): 4900 8.5 x 11" sheets per hour
Maximum Stock Size: 18"W x 25.5"L (45.7cm x 57cm)
Minimum Stock Size: 3.5"W x 5"L (8.9 cm x 12.7 cm)
Stock Weight: 12lb. - 18 point (45- 385 gsm)
Length: 60" (1.52m)
Width: 27" (0.69m)
Height: 46" (1.17m)
Weight: 250 lbs. (114 kg)
Perforation Options: 2,4,6,8,12 teeth per inch (TPI); 42 or 72 TPI MICROPERF
Rotary Score Options: wide (standard) or narrow
Strike Perf Attachment: Optional
Slitting Blade: Optional
Creasing Die: Wide (standard) or narrow
Impact creasing significantly reduces cracking of digitally-printed substrates during the finishing process.
Inverted AND regular impact creasing in the same pass!
Up to 10 impact creases per sheet.
Up to 20 jobs can be stored into memory.
Easy-to-use programming. Set up in minutes!
Rotary perforations (at the entrance of the machine for accuracy; no tail whip) are anvil style and produce a "burr-free" finish. Microperfs are also available.
Optional strike perf attachment available for "box" or "T" perfs.
NOTE: machines are pneumatic and require compressed air (compressor; not supplied) to operate.
GW-6000
The GW6000 is the most popular number/perf/score/slit machine in the industry. Operating at speeds of up to 6000 sheets per hour, the "6000" makes fast and easy work of finishing needs. With the ability to upgrade to another model at any time in the future, combined with a 5-year limited warranty, you can't go wrong with the "6000".
Features
Electrical: 120V/230V, 60/50Hz, 5.0 Amp
Maximum Stock Size: 18" x 18" (45 cm x 45 cm)
Stock Weight: 12# - 12 point (45 - 250 gsm)
Length: 44" (1.12m)
Width: 27" (0.69m)
Height: 16" (0.26m)
Weight: 106 lbs. (48kg)
Drive Unit Type: Electric Solenoid
Maximum Number of Numbering Positions: 10 per head per sheet
Maximum Number of Heads: 2
Repeat Action: Consecutive, 1x, 2x, 3x, 4x
Head Rotation: Lockable throughout 360 degrees
Numbering Heads: 6 digit standard (with 2 drop) 8 digit condensed optional "No" and letter prefix available
Impression Control: Electronically variable, crash up to 10 part sets
Inking System: Ink pad with reservoir
Perforating Options: 2, 4, 6, 8, 12 TPI
MICROPERF Options: 42 or 72 TPI
Scoring Options: Wide (standard) or narrow
Slitting Blade: Optional
Speed: 6,000, 11 x 8.5"/A4 sheets per hour
Minimum Stock Size: 3"W x 5"L (7.6 cm x 12.7cm)
Stand: Optional
Register: Microprocessor controlled to .010" (0.25mm)
Other Features:
- 6,000 standard-size sheets per hour
- Up to 10 numbers per head per sheet
- 1 or 2 numbering heads
- Heads rotate & lock throughout 360 degrees
- Tabletop model; optional stand available
- Crash number up to 10-part sets
- Feed sets from the UNGLUED or glued side
- Create "snap sets" while numbering
- Perforating options: 2, 4, 6, 8, 12 TPI
- Microperf options: 42 or 72 TPI
- Scoring options: wide (standard) or narrow
- Optional slitting blade available
- Ability to control depth of each perf/score/slit independently
- Automatic feed
- Accurate .010" register
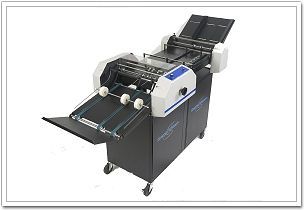
FINISHMASTER 150
From the floor model design with its 30-inch-long register board to the conveyor outfeed delivery, everything about the FinishMaster 150 spells productivity. Operating at speeds up to 20,000 standard-size sheets per hour, the "150" is ideal for mid to long-run finishing. Anvil-style perforation provides a burr-free flat finish. Blades can be changed in seconds, without removing any shafts. Production and value in one package.
Features
Electrical: 120V/230V, 60/50Hz, 3.0 Amp
Speed: 20,000, 11 x 8.5"/A4 sheets per hour
Length: 68" (1.73m)
Width: 27" (0.69m)
Height: 46" (1.17m)
Weight: 291 lbs. (132kg)
Maximum Stock Size: 18" x 18" (45cm x 45cm)
Minimum Stock Size: 3"W x 5"L (7.6cm x 12.7cm)
Stock Weight: 12# - 12 point (45 - 250 gsm)
Perforating Blade Options: 2, 4, 6, 8, 12, 16 TPI
MICROPERF Blade Options: 42 or 72 TPI
Scoring Blade Options: wide (standard), narrow, or double
Slitting Blade: Optional
Register Board: Yes; 30 inches long
Conveyor Outfeed Delivery: Standard
Other Features:
- Variable speed, up to 20,000 standard-size sheets per hour
- 30-inch-long register board for easy setup and perfect register
- Floor model on castors; doesn't need dedicated table or floor space
- Perforating options: 2, 4, 6, 8, 12, 16 TPI
- MICROPERF options: 42 or 72 TPI
- Scoring options: wide (standard), narrow, or double
- Optional slitting blade available
- Blade changes in seconds
- Ability to control depth of each perf/score/slit independently
- Automatic feed
- Conveyor outfeed delivery supplied standard
- 2 accessory holders supplied standard, each with one 12 TPI perf blade and one score blade.
CONVEYOR TRANSPORT SYSTEM
Stand-alone motorized conveyor system. It can be used to connect any machine to another, eliminating the need for additional handling. Its pneumatic cylinder allows for height adjustment from a low setting of 32" (81.25cm) to a maximum of 38" (96.5cm) with up to a 30-degree incline and decline. It enables machines of different heights to be easily connected. Variable speed control up to 20,000 sheets per hour.
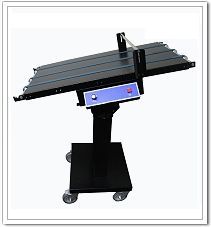
SPARE PARTS & SUPPLIES
UV COATINGS FOR
COMMERCIAL PRINTERS
UV coatings offer a highly attractive option for finishing commercial prints, facilitating the efficient production of impressively high gloss results. Moreover, they provide additional benefits. Unpleasant properties such as odor are minimized by advanced formulations and the use of outstanding raw materials. UV coatings are characterized by their fast curing time and low odor. They boast excellent flow-out, resulting in optically perfect surfaces, and demonstrate outstanding scratch and scuff resistance. Furthermore, UV coatings offer good running capabilities on most coating equipment. They provide high gloss levels with good flow characteristics, fast curing speeds to minimize infrared exposure, and excellent adhesion to most digital ink and pigmented systems. Multiple coating formulations are available, including high gloss, matte, satin, pearlescent, and transparent coatings.
APPLICATION & METERING ROLLS
Application rollers, akin to the tires on your vehicle, eventually require replacement or refurbishment. We provide the following services:
- Supply of new and refurbished rollers of all sizes for various popular roller coater manufacturers.
- Refurbishment of your existing application roller (this service typically requires one week to process).
CHECK OUT OUR
WIDE FORMAT DIGITAL INK OPTIONS
Our ink cartridges are specially formulated to precisely match OEM standards, ensuring seamless printer operation. There's no need to flush or perform any other special changeover procedures like profiling, etc. Simply order and use them to enhance your profits immediately.
Ultra Low Energy UV Curable Ink
Basic Description
National UV Supply's Ultra Low Energy UV Curable Inks leverage cutting-edge technology to facilitate rapid curing at minimal energy levels. This advancement enables NUVS users to reduce lamp power, expanding print media options for printers. Previously, some substrates were deemed too heat-sensitive for UV curable printing; however, with NUVS Ultra Low Energy UV Curable Inks, these media types are now viable. Additionally, this product offers enhanced abrasion resistance, adhesion, and overall performance for printed output. Ultra Low Energy UV Curable Inks cater to digital industrial and graphics applications and are compatible with printers such as Gandi™, Tekwin™, Vutek™, Durst™, Rastek™, Dilli™, Nur™, and Scitex™.
General Purpose UV Curable Ink
Ultra-Low Energy UV Curable Ink is specially formulated for high-performance, trouble-free printing. Our formulators' tight manufacturing specifications ensure consistent quality batch after batch. The value of NUVS inks is unmatched in the industry. NUVS inks offer an expanded color gamut, long-term outdoor durability, superior adhesion, and the lowest maintenance requirements of any ink in the digital inkjet marketplace. NUVS is setting the standard for the level of technical support and is unmatched by the competition. Ultra-Low Energy UV Curable Ink utilizes the latest technologies available to provide full cure properties at very low energy levels. This ink product expands the substrate choices for printers due to less heat being applied to the substrate during printing, where formerly, heat-sensitive materials could not be utilized with UV curable technology. This ink can be used on Flexible and Rigid Substrates.
Product Highlights:
- Premium Quality
- Best Value
- Consistency
- Superior Adhesion on Rigid Materials, including rigid PVC, Polystyrene, Polycarbonate, Acrylic, Foam Board, etc., and Flexible Materials, such as Pressure Sensitive Vinyl, Reinforced Banner, Canvas, Fabric.
- Performance includes Abrasion/Scratch Resistance, 2 Year Outdoor Durability, Optimized Printer Performance, Minimal Printer Maintenance.
- Typical Uses:
- POP displays, Outdoor Graphics, Billboards, Banners, etc.
Drying/Curing Parameters:
Ultra Low Energy UV Curable Inks are formulated to be fully cured when exposed to <200 mJ/cm2 from a medium-pressure mercury vapor lamp. The actual exposure needed to reach full state-of-cure will depend on the intensity and focus of the lamp system and spectral output of the bulb type; our highly experienced technicians can assist you in your system design and requirement.
Colors:
Cyan, Magenta, Yellow, Black, Red, Green, Blue, Orange, White, and Light Colors.
Handling & Storage:
All personnel handling the liquid ink should wear appropriate gloves and eye protection. Ink should be stored tightly closed with a room temperature range of 5-40°C (41-104°F). The shelf life of this product is 12 months from the Date of Manufacture. The ink should be kept away from UV light, direct heat, sparks, and flames. This product should be stored in its original packaging until the time of use.
Durability:
This product is 2-year outdoor durable.
Available Packaging:
This product is available in 1 Liter bottles. Custom packaging is also available.
Disclaimers:
National UV Supply Corporation stands behind the quality of its products. However, NUVS cannot guarantee the finished print output because we have no control over the printing equipment setup or process. While NUVS will provide sound technical advice on the use of our products, it is the user’s responsibility to ensure that the products being used are appropriate for the end-use application. All of the information contained within this technical data sheet is accurate as of the date published; this sheet may be updated or deleted as new information becomes available.
FlexiCure UV Ink
Ultra-Low Energy UV Curable Ink and FlexiCure UV Curable Ink are specially formulated for high-performance, trouble-free printing. Our tight manufacturing specifications ensure consistent quality batch after batch, setting the standard for ink value in the industry. These inks offer an expanded color gamut, long-term outdoor durability, superior adhesion, and minimal maintenance requirements. FlexiCure UV Curable Ink expands the applications suitable for UV Curable inkjet ink, providing adequate elongation and flexibility for fleet graphics use. Both inks can be used on Rigid Substrates, but FlexiCure is optimized for Flexible applications.
Product Highlights:
- Premium Quality
- Best Value
- Consistency
- Superior Adhesion on Flexible Materials such as Pressure Sensitive Vinyl, Reinforced Banner, Canvas, Fabric
- Performance includes Abrasion/Scratch Resistance, Elongation and Flexibility, 2 Year Outdoor Durability, Optimized Printer Performance, Minimal Printer Maintenance
- Typical Uses:
- Fleet Graphics, POP displays, Outdoor Graphics, Billboards, Banners, etc.
Drying/Curing Parameters:
FlexiCure UV Curable Inks are fully cured when exposed to ~300 mJ/cm2 from a medium-pressure mercury vapor lamp. Actual exposure depends on lamp system intensity and focus.
Colors:
Cyan, Magenta, Yellow, Black, Red, Green, Blue, Orange, and Light Colors.
Handling & Storage:
All personnel handling the liquid ink should wear appropriate gloves and eye protection. Store tightly closed at 5-40°C (41-104°F). Shelf life is 12 months from the Date of Manufacture.
Durability:
Both products offer 2-year outdoor durability, extendable to 5 years with a suitable laminate.
Available Packaging:
1 Liter bottles; custom packaging available.
Disclaimers:
While we stand behind our product quality, we cannot guarantee finished print output due to variations in equipment setup. It's the user's responsibility to ensure suitability for their application. Information in this data sheet is accurate as of the publication date; updates may occur.
LED Curable Inks
Natural Solvent Inks
Environmentally friendly ink solutions are crafted using natural materials like bio-solvents and water.
Premium BioSolvent Ink
Introducing Premium BioSolvent ink designed specifically for Wide Format and Super Wide Format printers. Offering outstanding performance on both flexible and rigid media, it seamlessly complements environmentally friendly media currently on the market. Derived from natural renewable resources, BioSolvents contain no Hazardous Air Pollutants or Heavy Metals. Ideal for a wide range of applications including Billboards, Banners, Point of Purchase displays, and Car Wraps, it's the perfect choice for companies prioritizing environmentally conscious advertising campaigns. Now available for Gandi™ and Vutek™ printers.
GlassBoost
Introducing a groundbreaking product featuring Glass Enhancing Technology, designed to enhance the performance of UV inks on glass substrates. Applied seamlessly via Inkjet directly to the glass substrate, this product works in conjunction with NUVS UV Curable inks, eliminating the need for curing or two-coating. With its one-step application process, printers can now achieve high-performance glass printing effortlessly, streamlining their workflow and delivering exceptional results in a single step.
GlassBoost is specially formulated for high-performance, trouble-free printing. Our formulator's tight manufacturing specifications ensure consistent quality batch after batch. The value of NUVS inks is unmatched in the industry. NUVS products offer an expanded color gamut, long-term outdoor durability, superior adhesion, and the lowest maintenance requirements of any ink in the digital inkjet marketplace. NUVS is setting the standard for the level of technical support and is unmatched by the competition. GlassBoost uses the latest technologies available to provide unmatched performance on glass when used in conjunction with UV curable inks. This product expands the applications suitable for UV Curable inkjet ink. GlassBoost provides an increase in adhesion, abrasion, and water resistance for UV Curable inks on glass.
Product Highlights:
- Premium Quality
- Best Value
- Consistency
- Superior Adhesion
- Can be applied via inkjet or aerosol spray
- Performance, Abrasion/Scratch Resistance, Optimized Printer Performance, Minimal Printer Maintenance
- Typical Uses:
- Graphics printed on Glass Substrates.
Drying/Curing Parameters:
GlassBoost is formulated to be fully cured during the printing process. The actual exposure needed to reach full state-of-cure will depend on the UV curable ink used and the intensity and focus of the lamp system and spectral output of the bulb type. Our highly experienced technicians can assist you in your system design and requirement.
Handling & Storage:
All personnel handling the GlassBoost should wear appropriate gloves and eye protection. The product should be stored tightly closed with a room temperature range of 5-40°C (41-104°F). The shelf life of this product is 12 months from the Date of Manufacture. GlassBoost should be kept away from UV light, direct heat, sparks, and flames. This product should be stored in its original packaging until the time of use.
Available Packaging:
This product is available in 1-liter bottles and aerosol cans. Custom packaging is also available.
Disclaimers:
National UV Supply Corporation stands behind the quality of its products. However, NUVS cannot guarantee the finished print output because we have no control over the printing equipment set-up or process. While NUVS will provide sound technical advice on the use of our products, it is the user’s responsibility to ensure that the products being used are appropriate for the end-use application. All of the information contained within this technical data sheet is accurate as of the date published. This sheet may be updated or deleted as new information becomes available.
Custom Industrial Inks
Our highly experienced development team is the perfect partner for any company looking to utilize inkjet technology in their industrial processes. We have a proven track record of developing functional products for manufacturing facilities. If you have an idea or a dream, contact us to bring it to reality!
EchoV Mild Solvent Ink
All the performance of solvent inks, made without harsh chemicals. Ideal for printers designed for mild solvent inks. Now available for Roland™ and Mimaki™ printers. EchoV Mild Solvent Ink is specially formulated for high performance, trouble-free printing. Our formulator's tight manufacturing specifications ensure consistent quality batch after batch. The value of NUVS's inks is unmatched in the industry. NUVS inks offer an expanded color gamut, long-term outdoor durability, superior adhesion, and the lowest maintenance requirements of any ink in the digital inkjet marketplace. NUVS is setting the standard for the level of technical support and is unmatched by the competition. EchoV Mild Solvent Ink uses the latest technologies available to provide Artifact-Free Printing. This ink product has all the performance of a full solvent ink, without the harsh chemicals, while maintaining a wide color gamut. This ink provides adequate elongation and flexibility for fleet graphics use.
Product Highlights:
- Premium Quality
- Best Value
- Consistency
- Superior Adhesion - Flexible Materials, Pressure Sensitive Vinyl, Reinforced Banner, Canvas, Fabric
- Performance - Abrasion/Scratch Resistance, Elongation and flexibility, 2 Year Outdoor Durability, Optimized Printer Performance, Minimal Printer Maintenance
- Typical Uses
- Fleet Graphics, POP displays, Outdoor Graphics, Billboards, Banners, Car and Bus Wraps, etc.
Drying/Curing Parameters:
EchoV Mild Solvent Inks are formulated to be fully dried post-printing using traditional printer-equipped heaters. There is no need for external drying devices even at the maximum print speeds advertised by the printer manufacturer.
Colors:
Cyan, Magenta, Yellow, Black, Red, Green, Blue, Orange, and Light Colors.
Handling & Storage:
All personnel handling the liquid ink should wear appropriate gloves and eye protection. Ink should be stored tightly closed with a room temperature range of 5-40°C (41-104°F). The shelf life of this product is 24 months from the Date of Manufacture. The ink should be kept away from direct heat, sparks, and flames.
Durability:
This product is 2-year outdoor durable, which can be extended to 5 years with a suitable laminate.
Available Packaging:
This product is available in 1-liter bottles. Custom packaging is also available.
Disclaimers:
National UV Supply Corporation stands behind the quality of its products. However, NUVS cannot guarantee the finished print output because we have no control over the printing equipment set-up or process. While NUVS will provide sound technical advice on the use of our products, it is the user’s responsibility to ensure that the products being used are appropriate for the end-use application. All of the information contained within this technical data sheet is accurate as of the date published; this sheet may be updated or deleted as new information becomes available.
Premium Solvent Inks
Outdoor durable Solvent Inks for Gandi™, DGI™, Tekwin™, and Vutek™ Superwide Format Inkjet Printers. High-Performance, Premium Quality Solvent ink for the wide and superwide format printing market. Premium Solvent Ink is specially formulated for high performance, trouble-free printing. Our formulator's tight manufacturing specifications ensure consistent quality batch after batch. The value of NUVS's inks is unmatched in the industry. NUVS inks offer an expanded color gamut, long-term outdoor durability, superior adhesion, and the lowest maintenance requirements of any ink in the digital inkjet marketplace. NUVS is setting the standard for the level of technical support and is unmatched by the competition. Premium Solvent Ink uses the latest technologies available to provide Artifact-Free Printing. This ink product brings the print quality to a new level when compared to OEM inks, while maintaining a wide color gamut. This ink provides adequate elongation and flexibility for fleet graphics use.
Product Highlights:
- Premium Quality
- Best Value
- Consistency
- Superior Adhesion - Flexible Materials, Pressure Sensitive Vinyl, Reinforced Banner, Canvas, Fabric
- Performance - Abrasion/Scratch Resistance, Elongation and flexibility, 2 Year Outdoor Durability, Optimized Printer Performance, Minimal Printer Maintenance
Typical Uses:
- Fleet Graphics, POP displays, Outdoor Graphics, Billboards, Banners, Car and Bus Wraps, etc.
- Drying/Curing Parameters:
- Premium Solvent Inks are formulated to be fully dried post-printing using traditional printer-equipped heaters. There is no need for external drying devices even at the maximum print speeds advertised by the printer manufacturer.
Colors:
Cyan, Magenta, Yellow, Black, Red, Green, Blue, Orange, and Light Colors.
Handling & Storage:
All personnel handling the liquid ink should wear appropriate gloves and eye protection. Ink should be stored tightly closed with a room temperature range of 5-40°C (41-104°F). The shelf life of this product is 24 months from the Date of Manufacture. The ink should be kept away from direct heat, sparks, and flames.
Durability:
This product is 2-year outdoor durable, which can be extended to 5 years with a suitable laminate.
Available Packaging:
This product is available in 1 Liter and 1 Gallon bottles. Custom packaging is also available.
Disclaimers:
National UV Supply Corporation stands behind the quality of its products. However, NUVS cannot guarantee the finished print output because we have no control over the printing equipment set-up or process. While NUVS will provide sound technical advice on the use of our products, it is the user’s responsibility to ensure that the products being used are appropriate for the end-use application. All of the information contained within this technical data sheet is accurate as of the date published.
UV Jet Recovery Fluid
UV Jet Recovery Fluid is specially formulated for high-performance cleaning of inkjet printheads. This product works to loosen partially cured ink and debris from the passageways which can then be removed from the printheads via fluid flow, pressure and vacuum. NUVS is setting the standard for the level of technical support and is unmatched by the competition. UV Jet Recovery Fluid provides superior value to the user by reducing printhead replacement frequency and cost.
Product Highlights:
- Premium Quality
- Best Value
- Can be used in many of the commercially available cleaning equipment.
- Performance - Unmatched recovery success rates, Returns the passages to “like-new” condition
Typical Uses:
Cleaning and Recovery of UV curable printheads.
Handling & Storage:
All personnel handling the UV Jet Recovery Fluid should wear appropriate gloves and eye protection. The product should be stored tightly closed with a room temperature range of 5-40C (41-104OF). The shelf life of this product is 24 months from the Date of Manufacture. UV Jet Recovery Fluid should be kept away from direct heat, sparks, and flames.
Available Packaging:
This product is available in 1 Liter and 1 Gallon bottles. Custom packaging is also available.
Disclaimers:
National UV Supply Corporation stands behind the quality of its products. However, NUVS cannot guarantee the finished print output because we have no control over the printing equipment set-up or process. While NUVS will provide sound technical advice on the use of our products, it is the user’s responsibility to ensure that the products being used are appropriate for the end use application. All of the information contained within this technical data sheet is accurate as of the date published, this sheet may be updated or deleted as new information becomes available.
BOOK A DEMONSTRATION AT
NATIONAL UV SUPPLY COMPANY
Experience the power of our cutting-edge printing solutions firsthand at National UV Supply Company! Would you like to see our coaters, feeders, creasers, in action? Perhaps you'd like to witness your substrate being coated, creased, or slit right before your eyes? Maybe you're eager to produce a job for your customer or receive training prior to purchasing?
Our demo facility is equipped to fulfill all these needs and more. You're welcome to visit us and coat your substrate using our two coaters (16" and 20") and Crease Master Pro, along with our deep pile feeder, all available for demonstration. Our equipment is user-friendly, so the majority of your staff can run it effortlessly.
When can you see it? Anytime! Simply contact our customer service department at 407-889-4874 to schedule an appointment for a personalized one-on-one visit. Don't miss this opportunity to revolutionize your printing processes with National UV Supply Company. Book your free demonstration today!
Contact Us TODAY
Fill out the form below, and a member of our dedicated team will be in touch soon to address your inquiry.
Contact Us
Frequently Asked Questions
Have questions about our services? We've got the answers you need.